4/1/2020
Expansion Stories
Jennifer Zurko
Michael’s Greenhouses | Cheshire, Connecticut
As of press time, Michael’s was just wrapping up building an additional 2 acres of gutter-connect, poly greenhouse from Westbrook. Owner Michael Arisco said that the business is coming off of record growth two years in a row, so they needed the extra space.
They have a very diverse customer group, said Michael, which includes big boxes, supermarkets and IGCs, so they needed more space for their annuals, specifically patio containers and hanging baskets. And since they’ll be growing more baskets, the new greenhouse will include new boom irrigation and a Boomerang hanging basket system from Greenhouse Technology, Inc.
Smith Gardens | Aurora, Oregon
Prins helped Smith construct 6 acres of open-roof greenhouses with diffused glass and a concrete cascade flood floor system from Zwart. Smith’s Site Manager Wes Bailey said that they’re in the final stages of installing a FormFlex hanging basket line with double rail booms from Cherry Creek Systems.
The expansion, which they’ve been planning for over a year, was required due to a couple of factors, said Wes.
“With our customers, the product size is getting bigger each year, as the consumers are wanting larger items from the garden center. These larger items take more square footage to grow and we need to have the ability to expand our sales during the peak season,” he explained.
Rainbow Greenhouses | Chilliwack, British Columbia, and Iron Springs, Alberta, Canada
This Canadian big box grower is again adding at two locations: 10 acres in Chilliwack and 15 acres in Iron Springs, which owner Stan Vander Waal says is Rainbow’s largest expansion ever.
They’d always had poly houses, but six years ago, they built an expansion with a glass Prins greenhouse. They really liked what they saw with regards to the plants’ performance, so all 25 total acres will be diffused glass greenhouses with ErfGoed flood floors when they’re completed in time for Spring 2021.
Pictured: Rainbow Green-houses is in the process of expanding at two locations. This one, which will be 10 acres, is at their site in Chilliwack, British Columbia. The inside will include new HPS lights, conveyers and ErfGoed flood floors.
“I have to say that we found from a growing point of view that crops tend to come a little bit earlier, a little more flexibility with regards to crops, the ability to manage the climate seems to be a little bit easier,” explained Stan. “And then when you think about all of the challenges around replacing poly, we just said let’s go this way. And after what we’ve experienced the last six years of growing under glass, we pretty much said we’re going to be glass from now on.”
Stan said that the biggest reason for the large expansion is because they’re experiencing growth across the board, from same-store sales compared year-to-year and even new business from existing accounts. Also, they had the space to expand—especially at the Iron Springs location, where only 40 out of the 160 acres is being used.
Plus, trying to contract out some of the excess material wasn’t an option. Stan said that many small growing operations that would have been potential contract growers have sold to the cannabis industry. And, really, many times, it’s just easier if you do it yourself. You have so much more control on everything, from the quality to the costs.
Rainbow has found this to be especially true with their houseplants program. Although Stan said all of their expansion decisions have been centered around annuals, which is where they’re seeing the largest growth, during the last three years, they’ve seen demand and sales for foliage plants double. And being the furthest point from Florida (besides Alaska), it just made more sense for them to grow indoor plants themselves.
“An average truck, if it has a team on it, takes three days to get here, but if it’s a single driver, you’re talking at least five days to get product here,” said Stan. “The deterioration that happens within that time, depending on the type of foliage, can be substantial, so there’s always shrink happening in that process.”
In the expansion from 2014, they tried LEDs, but were disappointed in the results and weren’t getting the return they were looking for, so HPS lights will be in all of the new greenhouses. This type of lighting allows them to use more for certain crops—like their increased foliage crop—but also control the costs.
“If we light [the foliage plants] up, we find that we can grow pretty much the same one we can buy out of Florida,” said Stan. “It’s been a really interesting surprise for us to see how many different items we can actually grow underneath the lights and see a very good response.”
Perino’s Home & Garden Center | Abita Springs, Louisiana
In October 2018, I visited Perino’s Home & Garden Center in Metairie, Louisiana, as part of the All-America Selections Summit in the New Orleans area (you can see some great displays and ideas in the Tricks section of the January 2019 issue of Green Profit). It was impressive, welcoming and very well-organized. At the time, I learned that all of their product is grown at an off-site location in Abita Springs, which is about 45 minutes north of New Orleans.
Third-generation owner Sal “Buddy” Perino said they grow 100% of their spring color in Abita Springs, with two trucks a day going back and forth to the store during peak. The Perino family bought the property in Abita Springs back in 1997 when the nursery business that was on it was selling. At the time, they were content with the space they had at another location 3 miles up the road, but the sellers were selling at a price they couldn’t pass up. It turned out to be fortuitous 20 years later as they’ve quickly run out of space.
“We’re maxed out with our poinsettias,” said Buddy. “And in the spring, we’re dealing with the same thing, so we really need the space.”
As of press time, Perino’s was in the process of building a gutter-connect, Z-top 35,000-sq. ft. greenhouse from Tubular Structures out of Mississippi that’s set to be finished by early summer. It has a special vented roof that raises up and overlaps to provide excellent ventilation, which Perino’s needs when growing in the hot and humid Louisiana weather. Gravel floors, concrete sidewalls, irrigation and heaters will be the finishing touches inside.
“We don’t stop growing; it’s not like we have a cut-off,” said Buddy. “We slow down in the summer and it picks up in the fall, but we have a lot things we have to put in when it’s extremely hot in the greenhouse—things like mums and poinsettias that you have to start when it’s hot to have for fall. So we needed a house that was very well ventilated. Cool pads only go so far.”
Now Perino’s total production under cover is now about 340,000 sq. ft. at both locations. Buddy explained that they not only needed to expand for their own retail location and their landscaper customers, but they’re currently in negotiations to sell to other local nurseries and garden centers. They’re also looking to get into online sales, too, at least locally. And as Perino’s staff expands with new employees and the third generation who’s transitioning into the business, they need to start looking for other sales avenues for their products, explained Buddy.
“It’s something we needed to do to try to figure out how to sell more product even with our retail store staying the same size,” he said. “We’re trying to look for other businesses that can buy our product.”
Winding Creek Nursery | Millbrook, Illinois
Since the Perkins family moved from Montgomery, Illinois, to the Millbrook location, they’d been selling plants outdoors off of hay racks out of the small hallway between the retail store and the older greenhouse.
“It wasn’t the best for the plants or the customers,” said Brian Monkemeyer, as any inclement weather meant that the plants had to be covered or moved, and the customers had to shop in the rain.
Pictured: Winding Creek Nursery grows and sells out of their new 17,000-sq. ft. DeCloet gutter-connect, triple-peak greenhouse, which has concrete floors, moveable retail benches, a vented roof and adjustable sidewalls. • Before the new expansion, Winding Creek used to sell plants outdoors off of hay racks out of the small hallway next to the retail store (toward the left)
And the greenhouse that was there faced the wrong way and was built on an incline with bad elevation, making it difficult to sell out of.
So a year ago, they had the old greenhouse razed and the land graded to put in a brand new 17,000-sq. ft. DeCloet gutter-connect, triple-peak greenhouse. And it’s ideal to serve as a retail space—the wide bays and concrete floors make it easy to push a shopping cart, and the vented roof and adjustable sidewalls allow for more comfortable temperatures inside.
“You have to think about the customer,” said Penny Monkemeyer, Brian’s wife and a third-generation Perkins.
The new expansion has more than doubled the space, said Brian, helping them to increase their production—now they grow about 50% of their own spring annuals.
“Business has been good, so we were able to make the investment,” said Mike Perkins, Penny’s brother. “And we were at the point on where we had to decide to do it or not.”
The construction of the new greenhouse also allowed Winding Creek to update their electrical lines (which Brian told us hadn’t been touched since the 1950s) and the water system with new storage tanks and pumps that gives them much better water pressure.
Brian and Penny—along with other members of the Perkins family, like Mike and his wife Tina—said they’ve learned a lot in the year they’ve had their brand-new greenhouse. Some things Brian said he would have done differently (made it bigger) and some decisions turned out to be the right ones (the concrete floors and moveable retail benches). But they’re very happy with how everything has turned out.
“Now people want plants even earlier,” Brian laughs. “And this makes it easier to do that. We don’t have to cover or bring the plants inside like we used to.”
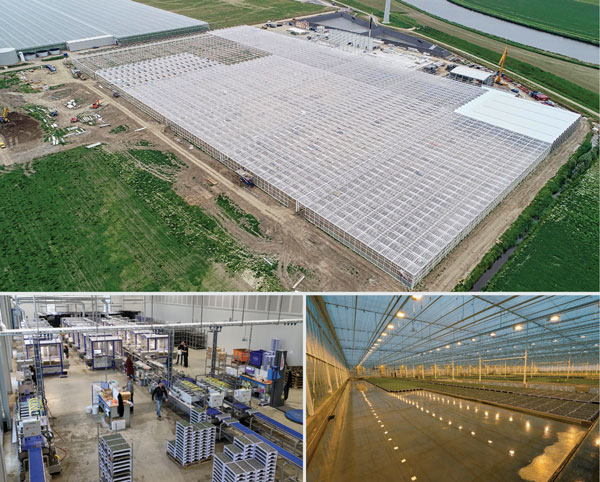
The World’s Newest Young Plant Range
Ever wonder what a Dutch propagator builds when they have a prime piece of property and a clean piece of paper? Young plant specialist Florensis needed a second location to dedicate to rooting vegetative cuttings. They moved in this past December and GrowerTalks stopped in in January to check it out.
Pictured: Florensis, during construction. • The Sticking Hall features 18 ISO Planters, plus manual lines and watering tunnels. Trays are filled off-site and trucked in as needed. • Greenhouses are just what you’d expect to see in the Netherlands. Upgrades over their old facilities include three layers of curtains and an extremely flexible fertigation system.
Florensis selected a 13-hectare (31-acre) site in Nieuw Prinsenland, a greenhouses business park in Dinteloord, south of Rotterdam, where they can share power and water infrastructure with several large greenhouse vegetable producers. (Their original location, 30 minutes away in Hendrik-Ido-Ambacht, will focus on seed plugs and elite stock.)
For a greenhouse, they chose a 6-hectare (600,000-sq. ft.) Ammerlaan Construction structure with two different glass roofing systems: 420,000 sq. ft. of Venlo-style roof and 180,000 sq. ft. of “cabrio” open-roof (for hardening off and growing cooler crops). The house is comprised of 17 different “compartments” (zones) to give a variety of growing environments. Bays are sized to the European standard: 12.8-meters (42-ft.) wide and 6-meters (19½-ft.) high to the gutter. Over the past decade, this height has proven to be optimum for the greenhouse climate, so growers aren’t experimenting much with ever-taller houses. Three layers of curtains provide blackout/light pollution, shade and humidity/heat retention.
Irrigation has been upgraded over their old location. A bank of 11 different nutrient tanks lets them custom blend virtually any feed—they currently use four different mixes, plus clear water. UV lamps provide disinfection to the irrigation water, while 13 holding tanks provide enough buffer to flood multiple bays at once.
Up front is a 45,000-sq. ft. office, processing hall and sticking room, the roof of which holds 1,400 photo voltaic panels that provide 100% of the power for the equipment below.
The Sticking Room is equipped with 18 ISO Planters, which can stick 40,000 cuttings per hour. There are also manual sticking lines, plus watering tunnels for all the trays. The Processing Hall is where product arrives and leaves.
There’s no soil mixing line; they decided to do all filling and tray disinfecting at the original location to avoid redundancy of equipment. They truck filled trays the 30 minutes from the home location as needed.
The most unsophisticated part of the facility is their internal transport system, which consists of forklifts and wooden pallets, plus standard plant trolleys. That’s almost humorous to see at Florensis, a business that in the 1990s was a pioneer in developing automated internal transport. But that fleet of tray-moving robots never really worked as well as they’d hoped. It turns out that a human is much less likely to drive through a wall. GT