10/1/2022
Lessons Learned in Automation
Jonathan Pedersen
(Editor’s note: This article is a recap of the talk Jonathan gave at Cultivate’22.—JZ)
Automation is a hot buzzword in our industry these days, but the process of incorporating automation into your nursery processes is complex. One of the first lessons we learned about automation is that you never stop learning. It’s an ongoing process—one that is very specific to your organization, your facility and your employees.
Over the last decade at Monrovia, we’ve focused on ways we could use advanced technologies to complement our hand craftsmanship. Our horticultural craftsmen are essential to our business. Their passion for plants, expertise and experience allow us to grow the highest-quality trees, shrubs and perennials in North America. That personal touch isn’t something you can replace. We didn’t want to change who we are and what we stand for, but we wanted to change how we accomplished some of the tasks that took too much time and had less value. It wasn’t the people that needed to change, it was the process.
Pictured: Monrovia uses an Orlandi Walk Behind Conical Pruner, which allows them to tip-prune shrubs with one person instead of six.
Why automate?
One of the top reasons nurseries in the U.S. are turning to automation is labor concerns. Minimum wage increases, concerns about government labor program availability, lack of people to do the job or increased turnover all rank as top problems that automation could potentially solve. But there are other drivers. At Monrovia, we looked at the human value of each task, asking ourselves three questions:
• Is this a job that’s best completed by a human being? Is it a job that can only be done by our craftsmen?
• Is it meaningful and fulfilling work that requires skill?
• Is this task a safety concern? Is it repetitive and may cause injury?
When you think about automation, the first thing that may come to mind is speed. It makes sense that technologies will make the process faster. But, for Monrovia, we wanted to ensure automation was making things better. The questions above gave us a place to start. It allowed us to create a list of tasks we thought could benefit from new technology.
Where to start
When it comes to automation, the big picture is just that—really big. That’s why it’s important to start with a small project, get a win under your belt and then move on to the next opportunity.
The first step is to develop a way to measure the impact of the project. If you can’t measure it, you shouldn’t be doing it. Data will help you understand if automating is really helping your bottom line. You need to have an ROI (return on investment) model. Even a simple ROI formula will help visualize progress and help determine if the project makes sense. Ask yourself these questions:
• What’s the capital outlay for the project?
• Determine what the payback of the process is for you and decide what success looks like. Is your payback cost savings or process improvement? How will this change your business? (We developed a three-year benchmark. If we couldn’t see the benefits in under three years, we re-evaluated.)
• Can you easily measure the results and the effect of the project? Again, if you can’t measure the results of a project, you shouldn’t be doing it.
• What other process changes will be necessary? What other areas of your business will be involved?
Our approach to automation is focused around our Monrovia Nursery Quality “MNQ” philosophies, which incorporate the principles of Lean Six Sigma in which you: Define, Measure, Analyze, Improve and Control the project area.
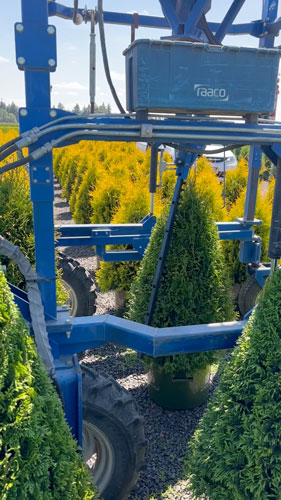
Time, training & tools
It’s important to have a realistic understanding about how much time and resources you’ll need to devote to your automation project. One of the biggest lessons we learned is that it always takes more time than you initially think. If you believe the project will take one year to implement, it will more realistically take two.
Training and maintenance are two other important factors relating to time. Many of the machines and technologies are coming from Europe, which can create some challenges. First, European nurseries are very different from ours in North America. They’re typically smaller and often they’re growing one type of crop and/or pot size. We’ve also found that the machines aren’t as strong as we need them to be. We’re frequently modifying and reinforcing them after we purchase.
Pictured: Larger conical pruners offer better tipping for larger varieties and more consistent-looking shrubs.
The second challenge is with labor skill and training. Employees will need to be trained on the equipment, which takes time. Often these machines are using computers, so they require different skills. If they’re integrated into your network, they also can take time away from your IT department.
These machines also have different components including eyes, motherboards and many, many belts. Having a plan to deal with breakdowns and technology issues is critical. Downtime takes away from your ROI. If your parts and service sources are overseas, they’re in a different time zone. You can’t rely solely on the manufacturers for support; you need to be prepared to solve issues on your own. Make sure you stock up on spare parts to avoid shipping delays. Tinker, adjust, fix and don’t give up.
Activate employee experts
Many of the new technologies we’re using at Monrovia are customized. Our team works together to rebuild or modify many of the machines to make them work for our specific needs. We have multiple employees trained on each machine and they become experts for that technology.
We install hour meters on all our equipment to measure their use. We also have monthly team meetings to analyze the effectiveness and review the data. We’re constantly thinking about how we can make the tools work smarter, increase our efficiency and help our employees work better, and it’s important to note that many of the best ideas have come from our employees doing the job. Make sure you’re encouraging innovation and rewarding their success.
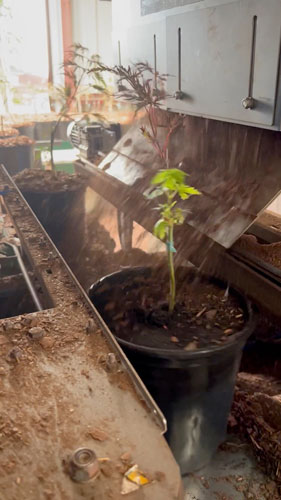
Nursery automation examples
Our Orlandi Walk Behind Conical Pruner is easy to use, lightweight and maneuverable. It was actually too lightweight at first. We had to rebuild the frame to make it stronger. This machine allows us to tip-prune a field with one person instead of six. And it allows us to prune more often, which creates a better flush and provides a consistent look across all the shrubs. This is a good example of automation not just doing things faster—this machine helps us improve the quality of our plants.
Monrovia uses an Orlandi Walk Behind Conical Pruner, which allows them to tip-prune shrubs with one person instead of six. Larger conical pruners offer better tipping for larger varieties and more consistent-looking shrubs.
Pictured: Monrovia tops all of their containers with bark to reduce the need for pre-emergent herbicides and to keep the soil moist.
We’re also using larger Lomers upright conical pruners that allows us to do lighter tipping more often for larger upright varieties. Our conifers grow better with this technique and we’re able to supply our customers with higher-quality, consistent-looking plants.
Our Bark Toppers are another example of automation that allows us to improve the quality of our plants. This process is an extra step at canning, but it produces great results on multiple levels. Adding the mulch to the top of our cans reduces the need for pre-emergent herbicides, helps keep moisture in the can and keeps a nice, clean look. It took some trial-and-error to get this machine working correctly, but it pays off in reduced use of chemicals.
Don’t give up
Make sure your employees know they’re always going to be your biggest asset. They need to know the why and not just the how of your automation project. Your goal is to improve their jobs, not eliminate them.
Expect some failures and misses. The key is not to give up. The solution will likely come from your employees, trial-and-error and perseverance.
As our industry continues to embrace these technologies, it’s important that we continue to share the lessons we’re learning. It will make us all better growers and that’s good for everyone. GT
Jonathan Pedersen is CEO and President at Monrovia Nursery Company.