1/1/2020
Making, Mixing or Buying
Dr. Brian E. Jackson
The growing media industry continues to evolve and grow in some pretty exciting and innovative ways. From coast to coast and from continent to continent, the advancement in growing media offerings are equipping growers to be more successful and profitable.
Figure 1: Wood substrate components vary in their manufacturing processes, particle size and shape, and color, as well as the ability to be easily mixed.
Regarding the development and commercialization of wood substrate components, the number of product offerings and company options has increased rapidly in the past 18 months (Figure 1). The “trend” of using wood components in our growing mixes has moved beyond “trend” and into more of a “mainstay” reality. While still a very new material to many in the industry, enough is known about the potential of wood and enough growers are using it successfully across the globe (hundreds of growers growing millions of plants in wood substrates) that there’s now some confidence regarding the future of these materials. Below are several options available to you.
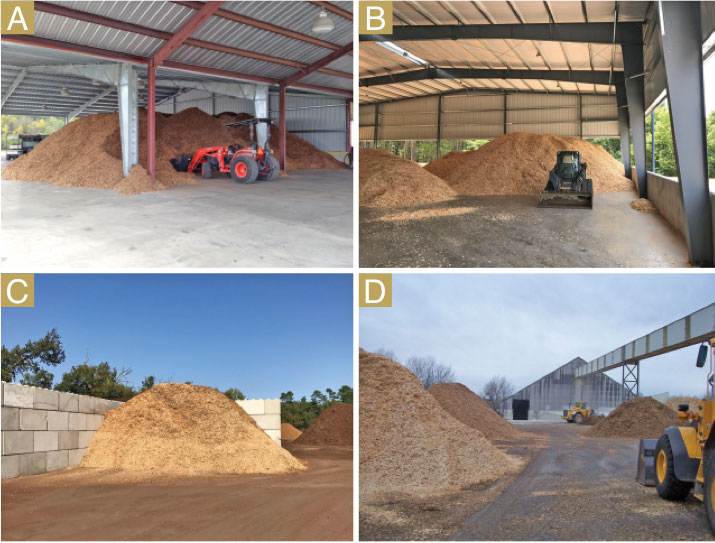
Making wood substrates
The past decade has seen several growers make the decision to produce their own wood substrate materials. Beginning with Young’s Plant Farm in Auburn, Alabama, other large and even some smaller operations have been successful in this endeavor.
Figure 2: Wood chips to be hammer-milled should be stored under shelter (A and B) to prevent being rained on, while wood chips destined for other processing methods can be left outdoors (C and D).
There can be big advantages to making your own wood substrate, especially if you own property with pine trees (mostly loblolly—Pinus taeda) or have close access to reliable and abundant quantities. The utilization of existing wood resources, plus the complete control of the harvesting and processing of the materials, can give you a lot of flexibility, not to mention savings.
If land/trees aren’t owned, then they have to be sourced from some forestry industry or individual. Aside from locating and securing quality tree resources, there are a lot of up-front costs and operating variables that can present challenges to making your own substrate. Despite the initial costs and annual substrate production expenses, the savings of making and using wood are reported to be substantial, with investment costs being returned within three to five years.
To make your own wood substrate, as discussed in previous articles, there are several methods/processes that can be employed—mainly hammer mills, screw extruders or disc refiners. Currently, the growers manufacturing their own substrates are using hammer mills. Hammer mills are cheap and readily available compared to the other machinery types.
After acquiring trees/wood chips and a mill (or other machine) for processing there are other expenses, including building/shed, tractor, super sack (tote) fillers, conveyors, personnel, training, storage facilities, etc. The wood chips to be hammer-milled (whole tree chips or pulp chips) need to be stored dry (as can be seen at Young’s Plant Farm in Figure 2A and American Color Greenhouse Figure 2B).
The need for keeping the wood chips dry relates to the inability/difficulty in milling wet wood chips. Wood chips used in the production of commercial wood fiber substrates that use processing equipment other than hammer mills do not have to be kept dry because the moisture doesn’t negatively affect the processing like it does in hammer mills. Wood chip storage outdoors is common at facilities that use twin-disc refiners (Profile Products—HydraFiber; Pindstrup—ForestGold; Kleeschulte—Topora, etc.) or extruders (Klasmann—GreenFibre; Florentaise—Hortifiber; Floragard—Florafibre, etc.) as seen in Figures 2C and 2D.
Figure 3: Once processed, some wood components should be stored in totes (A) or under shelter (B) to keep dry, while other products can be left outdoors (C and D).
After the wood products are manufactured, they have to be stored under adequate conditions until they’re used. The storage method and duration can vary depending on greenness of wood chips, method of wood processing, time of year, etc. If storage indoors or in totes is required/suggested, there is, of course, space needed to accommodate this. Pine tree substrates (hammer-milled products) are most often stored in totes to age and can be covered (Figure 3A) or uncovered. Other commercial wood fibers are also kept protected from rain after production (Figure 3B). Others, including sawdust that’s used at some greenhouse operations (Figure 3C) and fiber-peat blends (Figure 3D), can be stored outdoors due to their ability to be mixed/blended adequately even if wet.
The up-front capital costs associated with equipment, facilities and personnel needed to make wood substrates have mainly limited this option to larger growers. That could change in the future if growers were to form cooperatives to achieve their substrate processing needs while distributing the costs. The other potential downside to making your own substrate is the lack of technical support and analytical services that most always accompanies commercial products. If a substrate-related problem arises during crop production, the grower is now “on their own” or needing to hire an outside consultant to assist.
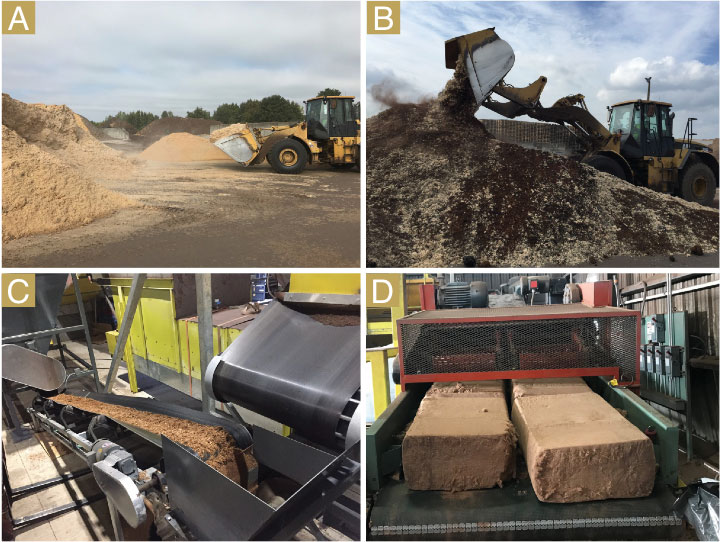
Buying wood products and mixing your own
One of the more recent options for growers is the availability of commercially produced wood products that can be purchased and then mixed “in-house” at the grower’s facility. Wood fiber as a component is no different than peat, coconut coir, pine bark, perlite, etc. in that it can be bought as a sole ingredient and then used to formulate the mix needed or desired by the grower.
Figure 4: All wood substrate materials cannot be blended with other materials the same way. Different techniques—including pad mixing with loaders, conveyor mix lines or specialized fluffing/blending equipment—are among the options for mixing.
All wood products aren’t packaged, delivered, stored or able to be mixed with other materials (peat, bark, coir, etc.) the same way. Some wood products blend easily and uniformly with other materials and can be pad-mixed with front end loaders (Figures 4A and 4B). These include any hammer-milled products, most screw-extruded products, sawdust materials, and in some cases, even specially treated disc-refined fibers. Other than pad mixing, growers may elect to use batch mixers with continuous ribbon turners or paddles, cement/rotary mixers or conveyor in-line mixing systems (the most advanced, technical, precise and expensive method) as seen in Figure 4C.
Any of these methods should work well if the wood component mixes easily. Some wood fiber materials, mostly those manufactured by disc-refiners, are extremely uniform, “fluffy” or “wooly” in nature and can often aggregate into balls (especially when wetted) and not mix very well with traditional systems or methods. Products like HydraFiber, which come in compressed bales, need to be loosened (re-constituted) before then being blended with peat or other materials using unique equipment that’s been designed specifically for this purpose (Figure 4D).
Wood products in compressed bales can be very desirable in that there’s reduced storage space needed at grower operations, reduced transportation costs, ease of handling, etc. Compressed bales of wood fiber have been used for many years in the hydro-mulching and insulation industries and now the benefits are being expanded to growing media industries.
Figure 5: Commercial wood fiber suppliers currently offer various sizes of compressed bales, including towers (ForestGold—A), smaller bales (HydraFiber—B) and coconut coir wood blends (Florentaise—C).
Currently, Pindstrup is offering compressed tall bales/towers of ForestGold wood fiber, which yield approximately 15.5 cubic yards of wood fiber (12 cubic meters) when loosened using any standard bale fluffing/busting equipment (Figure 5A). Profile Products offers five different grades/sizes of Ultra wood fiber in compressed 50-pound bales (13:1 expansion rate yielding about 24 to 28 cubic feet), which use their specialized fluffing equipment for expansion and mixing (Figure 5B). Profile also offers Hybrid and EZ Blend mixes, which don’t require the use of specialized equipment. Other interesting and very unique products currently only available in Europe are wood: peat bricks and bales offered by Florentaise in France (Figure 5C).
Buying ready-to-use products
Maybe the most popular option is the purchasing of pre-formulated and packaged mixes that are ready to use upon delivery. Among the current options available to U.S. growers are products that contain several different types of wood materials from many different resources. Choosing this option doesn’t require any specialized equipment, extra storage space, material handling or management, ingredient decisions or formulations, trained personnel, etc., and they most always come with the full technical support of the supplier. Many companies offer products containing wood materials, including Oldcastle, SunGro, Berger, Lambert, Klasmann, Pindstrup, Profile and others.
In summary, there are many variables to consider when deciding whether to make your own substrate materials, buy commercial wood products and blend in-house, or buy premixed ready-to-use substrates. There are more challenges, potential benefits and variables than those mentioned in this article. Additionally, there’s a lot more detail to those topics mentioned here, but couldn’t be fully elaborated on.
As is true with most big decisions, a lot of homework is needed before choosing which option is best; however, be delighted in the fact that there are several good options to choose from! Many substrate companies offer online calculators and other services to aid growers in making decisions regarding whether to make their own mixes or buy pre-formulated ones. As more research is conducted and more is learned about the processing, handling, storage, mixing and behavior of wood, expect to see more products on the market and more processing opportunities arise. GT
Brian E. Jackson is an Associate Professor and Director of the Horticultural Substrates Laboratory at NC State University. Brian can be reached at Brian_Jackson@ncsu.edu.