8/27/2015
Growing Pains
Chris Fifo
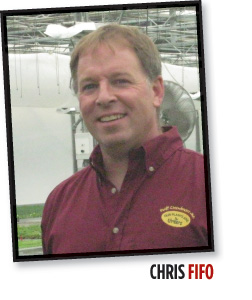
As I write, this summer is coming to a close and I’m still recuperating from our vacation to the Boundary Waters of Northern Minnesota. When my parents retired more than 20 years ago, they built their dream home in the forest on Farm Lake just outside of Ely.
I cherish the time I spend there and it’s always a joy sharing it with others. This year, I was blessed to share it with my girlfriend for the first time and my son brought his best friend along as well. However, I was sad that my daughter had to work and couldn’t make it. It was the first family vacation she’s missed. I knew it was coming, which is why we did the Grand Canyon and Las Vegas last year, but it doesn’t make it any easier.
Change can be difficult and growing can be painful, but they’re both inevitable. All we can do is plan for it and prepare ourselves the best we can—especially when it comes to adding more growing area. When is the right time to build?
For years we’ve experienced a steady growth in perennial sales and production numbers have long since surpassed available space at times. Each fall, we rent space from Goode’s Greenhouses about 45 miles away when we reach capacity. Last year, we brought them 25,000 trays of 50 plugs, then brought them all back when space opened up here.
When I add up just these transportation and rental costs, it makes good economic sense to build, but there are many more considerations and discussions to be had before we add more production area.
First and foremost is quality. Can we add another 30,000 sq. ft. and still maintain our high standards for quality? In my opinion, as far as our fall 50-plug production goes, it may actually enhance quality. Picking up, stacking and transporting 25,000 trays to another location and back certainly takes its toll on the crop. If these could be grown and finished here, under our daily watchful eye, all the
better.
But whose watchful eye would it be? That’s another issue to be considered. Do we have the grower staff to cover another range? The answer to that is not right now. We would likely need another assistant grower and another full time “horticultural professional,” as I like to call them. A plant nerd with the passion. We recently hired an assistant, but are still looking for the “nerd.”
The next big question: Is this growth sustainable? Will the demand for our perennials, herbs and edibles continue to grow? Will we not only be able to fill this additional space with finished material in the spring, but also sell it? We would need to get out our crystal ball to answer that question.
The past four seasons in a row we’ve enjoyed strong finished sales and could have used the extra space. However, we’ll never forget the spring of 2011 and the amount of leftover material we had that year. We’re all at the mercy of Mother Nature and her unpredictability when it comes to spring sales, so it’s anyone’s guess.
Okay, so what if we can fill it up and have the increased demand for our potted plants? Will we be physically able to pull those additional orders during peak days and weeks? The way I see it, the extra space should allow us to keep our crops more organized, at least at the beginning of the season, i.e., herbs together, annuals, 6-in., veggies, etc. This should make order pulling more efficient, but we would likely need another team.
And finally, will we be able to get that additional product to our customers on time? We deliver our finished material ourselves and don’t usually rely upon outside carriers, except for the pallet shippers. Will we have the labor to get the trucks loaded? Will we even have enough trucks, for that matter?
So many questions and so many unknowns. What about infrastructure? Will we have enough water pressure? Will we max out our fertilizer injectors? Will we need additional warehouse space?
So many things to consider … I think I need another week floating on the lake with a cocktail in my hand to think about this!
GT
Chris Fifo is Technical Services Advisor for Swift Greenhouses, Inc. in Gilman, Iowa.