6/1/2019
The Economics of Lighting Young Plants Indoors
Paul R. Fisher, Celina Gómez, Megh Poudel & Erik Runkle
With any economic analysis, the devil is in the assumptions. In this article, our goal is to help provide you with a framework on how to evaluate costs and profitability. First, we’ll go through an example of a plant factory based on Japanese research, highlight two U.S. grower operations and then provide a prototype approach you can adapt to test performance and profitability.
A lettuce indoor plant factory case study
Japan has been the leader in indoor plant factory research and development. We highly recommend “Smart Plant Factory” edited by Dr. Toyoki Kozai and others as a reference. In this eBook, Dr. Uraisami estimated costs for a 1,000 m2 (10,764 ft2) lettuce plant factory that had six shelf layers of production to provide 2,183 m2 (23,498 ft2) of cultivation space. This approximately $2.2 million (USD) facility would have the capacity to hold 14,686 propagation trays with 11 in. x 21 in. dimensions (1.6 ft2) if adapted for young plants.
Table 1 shows a few summary figures for the operation. About 30% of the initial investment cost was in LED fixtures, sufficient to provide 100 µmol/m2s of photosynthetically active radiation (PAR), with the remaining 70% in other material and facility costs.
Electrical operating cost from LEDs to run at 100 µmol/m2s of PAR for 16 hours per day would add $0.18 per tray per week from this partial budget, assuming a U.S. average $0.105/kWh for February 2019 commercial electricity rates from the U.S. Energy Information Administration. This light level and duration, which would provide 5.76 mol/m2d of daily light integral (DLI), is a reasonable assumption for young plants, but at least twice this DLI would typically be required for lettuce and other edible crops.
Although costs will vary for a purpose-built facility for young plants, the lettuce example highlights several points:
• There’s a high capital cost per unit area of production and LEDs are only one component of investment costs. A complete budget would include the building itself, an HVAC system, carts, racks, shelves, an irrigation system, environmental controls (carbon dioxide, temperature) and plant-processing areas.
• Electricity is a major operational cost. Japanese researchers find that lighting typically requires about 75% to 80% of the electrical cost, with about 15% to 20% cooling in a well-insulated room, and the remainder to run fans and pumps. The efficacy of lighting fixtures (efficiency of converting electricity into photons) selected for the operation is therefore especially relevant for indoor production.
• Carbon dioxide (CO2) isn’t included in Table 1, but is a minor cost (about $1/ft2 per year) in a tightly insulated growth room that has 0.02 or less air turnovers per hour.
• Labor efficiency is just as critical in an indoor facility as in greenhouse production. Labor savings can occur from automation, reduced need for pest and growth control activities, and more standardized operations. However, product handling and flow must be labor-efficient. For example, if plant products are moved on carts into a cramped modified shipping container with a single entrance and exit, work efficiency is likely to be difficult.
Commercial indoor young plant operations
We’ve been fortunate to learn from Battlefield Farms and Shenandoah Growers in Virginia, who are pioneering indoor young-plant production. Battlefield Farms installed a system initially to improve rooting success of high-valued heuchera tissue-culture transplants and have now expanded to other crops.
Shipping carts are wheeled into a modified seed germination chamber (Figure 1). LEDs are mounted in bays to light either from the sides or above each shelf on the carts. Average light level is 100 µmol/m2s of PAR for 12 to 24 hours, resulting in 4.3 to 8.6 moles/m2d.
Shenandoah Growers use indoor growing to start many of their seed herb crops and also to produce micro-greens. They have a purpose-built facility, including automated subirrigation. (You can see an excellent video about the operation at www.youtube.com/watch?v=DTFWSOca080.)
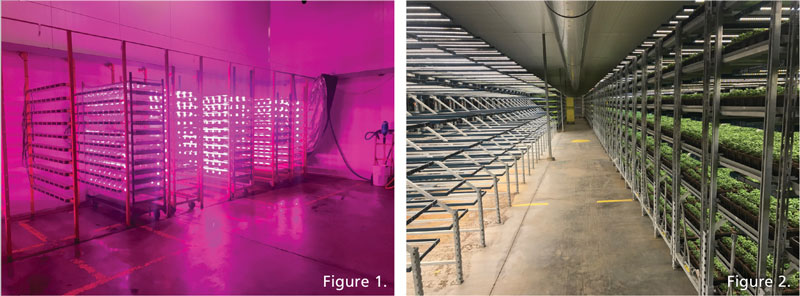
Figure 1. The enhanced rooting chamber at Battlefield Farms in Virginia. Shipping carts of young plants are lit by LEDs mounted horizontally in bays.
Figure 2. Starting herb seedlings indoors at Shenandoah Growers in Virginia
Applying these concepts to a prototype for testing
Based on these large-scale commercial designs (Figures 1 and 2), at the University of Florida we’re taking a prototype approach (Table 2). A single shipping cart is being modified for placement in a temperature-controlled room such as a germination chamber.
We’ve purchased a shipping cart with 10 solid shelves to be wheeled into a light metal bay structure mounted with LED fixtures similar to Figures 1 and 2. We’re evaluating different LED options—for example, a system with three LED strips per shelf consuming a total of 90W, dimmed by 48% to provide 100 µmol/m2s. Electrical costs for the LEDs for Table 2 are calculated based on the total wattage (90W x 10 shelves) x the dimmer level (48%) x 16 hours/d x 365 days per year x 50% assumed use/1,000 = 1,261 kWh @ $0.105/kWh = $132 per year.
Table 2 has conservative (high) cost assumptions—we believe that the investment cost of $5,517 per cart could be reduced with design improvements and volume discounts. In addition, we assume that the shelves average only 50% full during the year because of seasonality, whereas maximizing capacity would decrease the investment cost per tray. However, Table 2 doesn’t include all overhead and capital expenditures needed in a complete vertical farm, such as heating and air-conditioning.
Adapt Table 2 for your own design. Alternative technologies are available, such as LEDs mounted on strips and panels. Make sure the LED option you choose has a high fixture efficacy (more than 2.0 µmol/J), is designed for a humid environment and has a suitable spectrum as described earlier in this article series.
Ultrasonic fog can be added to this structure for humidity control. Plants are hand-watered in this prototype (which is the approach at Battlefield Farms), but subirrigation could be added (as used in Shenandoah Growers).
We can divide the annual costs in Table 2 ($1,494) by the number of trays that can be grown (we assume 60 trays per cart at any one time x 52 weeks/4-week crop time x 50% use = 390 trays per year). That gives $1,494/390 = $3.83 per tray, or $0.013 per plant if you grow 288 plants per tray. A simple way to interpret Table 2 is that each tray costs approximately $1 per week (rounding up from $0.96) to grow indoors.
Are we making money yet?
With young plants, there are several ways to evaluate profitability from indoor growing. One approach is to calculate how benefits in reduced crop time or reduced crop shrinkage (losses) might exceed the cost of $3.83 per tray over four weeks in Table 2. Crops that have a high sales value, small size, and either high shrinkage rate or slow rooting time in the greenhouse are good candidates for indoor production.
Break-even reduction in shrinkage: There’s an economic value from plants that successfully root indoors that would otherwise die in the greenhouse. A break-even number of extra saleable plants (i.e., the reduction in shrinkage) can be calculated that would pay for the extra cost of indoor production compared with lower greenhouse cost. This number equals the additional indoor production cost per tray/sales value per plant.
At UF, we’ve been working with tissue-culture blueberry microcuttings in 288-trays grown for four weeks indoors with a sales value of $0.60 per plant. In that case, $3.83 cost per tray to grow indoors (from Table 2)/$0.60 = 7 extra plants per tray (3% less shrinkage in a 288 tray) to pay for the additional production cost indoors. We’ve easily exceeded this threshold for blueberries.
Reduced crop time: The crop time for blueberry in a 288-count tray in greenhouses during the summer is around 10 weeks. In four weeks, we can root the plants indoors and finish them for two weeks in a greenhouse. Starting young plants indoors, and then finishing them in a lower-cost greenhouse, means that we can increase the turnover of plants and reduce cost. By reducing greenhouse production time from 10 to two weeks, there’s five times the potential crop turnover (and net profit) in the greenhouse. If the net profit from growing other crops for eight weeks in the open greenhouse space exceeds $3.83 per tray, that would more than pay for the indoor space.
In conclusion
In this article, we’ve provided information that you can adapt to analyze costs and profitability of indoor growing of young plants. We encourage you to do your own calculations and test this emerging technology in your operation. GT
References: T. Kozai (ed.) 2018. “Smart Plant Factory”. Springer, https://doi.org/10.1007/978-981-13-1065-2.
Acknowledgements: We thank our industry partners at the Floriculture Research Alliance (floriculturealliance.org), and the USDA Floriculture and Nursery Research Initiative for funding this research.
Paul Fisher is Professor and Extension Specialist (pfisher@ufl.edu), Celina Gómez is Assistant Professor, and Megh Poudel is a Ph.D. student at the University of Florida. Erik Runkle is a Professor and Extension Specialist at Michigan State University.
