4/1/2023
Consistent, Relentless Improvement
Bill Calkins
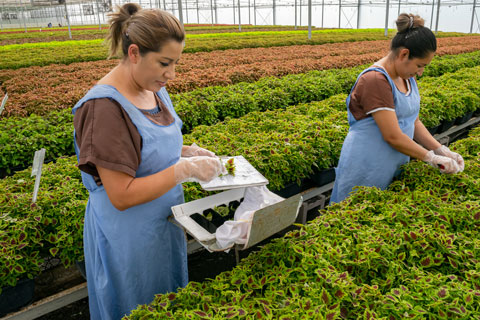
When a box of cuttings arrives on your loading dock and gets unpacked, the hard work of producing a top-notch crop for wholesale or retail sale begins. Or does it?
A lot of work has already gone into those little plants, often hundreds or thousands of miles away at a farm in another country. Offshore production might seem like a mystery if you haven’t had an opportunity to visit such a facility, but high-tech production, specialized facilities and entire workforces of well-trained and very proud growers worked behind the scenes to fill that box and supply you with what’s needed to achieve success.
Pictured: Dedicated scouting teams and constant quality monitoring are critical to our industry’s leading off-shore producers. Here are Dümmen Orange team members trained in quality control.
From new greenhouse technology and computer systems to tighter sanitation protocols and sustainable shipping, improved plant health are very clear common goals between all breeders. But other game-changing upgrades to worker health and safety, chemical reduction, onsite testing labs and expanded product ranges have been launched in recent years, adding value to the products you purchase.
Facility & logistic upgrades
As the list of products produced by offshore suppliers increases and technology leaps forward, greenhouse facilities evolve and supply chains improve. The health and quality of young plants from farm to customer is paramount. This means investments must be made every fiscal year.
“We are in the process of replacing our greenhouses and bringing them up to the newest standards,” said Michel Zevenbergen, Florensis technical crop manager. “The new greenhouses have a 6-meter gutter height; thus, we have increased our air buffer, which results in a more stable climate. We are also furnishing them with our newly designed growing tables fitted with a water recirculation system.”
A better climate and higher hygiene levels improve the plant quality and lower the disease pressure, he said. The new water recirculation system allows Florensis to make much more economic use of water and fertilizer.
Mike Klopmeyer, president of Ball FloraPlant, explains the company’s newest farm (YecaFlora) under construction in Central Mexico will benefit in many ways from its location.
“New farms are all about location, location, location,” he said. “YecaFlora will benefit from a perfect climate for key crops during peak season [i.e., geraniums December through March and poinsettias June through August], readily available labor for harvesting, and most importantly, complete control of cool chain since product can be trucked to the U.S. border on refrigerated trucks and via direct flights from Mexico City into major Canadian cities.”
Pictured: Off-shore farms like Ball FloraPlant’s Las Limas facility in Nicaragua continue expanding to serve the North American market.
Like in all aspects of business these days, flexibility and nimbleness are critical. Dennis Hitzigrath, general manager and co-owner of Vivero, shares that the company “has built some new, taller greenhouses, which will help us maintain better conditions for our crops, allowing us to produce better quality cuttings and have more growing climate flexibility for producing an ever-increasing list of species.
“We are proportionately shipping a lot more with temperature-controlled trucks. Trucking is very reliable and will keep the cold chain, making sure the cuttings arrive in better condition at our customer’s door.”
Start clean, stay clean
The absolute highest levels of sanitation are crucial for offshore producers sending young plants to the North American market. The protocols in place at the farms are truly next-level.
Mike Fernandez, North American market manager at Danziger, explains the company’s entire facility was built around sanitation protocols.
“When employees enter the facility, they are divided into groups, and at this point, the employees working in the highest-protocol crops like petunias and calibrachoa shower and change into company clothes supplied fresh every day.
Each of these areas has its own set of protocols depending on the crop, he said. “They are not allowed to change work areas at that point and employees are not allowed back out of the facility until they go home.”
Beyond sanitation strategies for workers, disease management and testing protocols at offshore farms have reached incredible levels in the past few years. A lot of this is due to new technology, as well as major investments in grower training and systems.
Nathan Sells, managing director for annuals, perennials, pot plants and sales for Dümmen Orange feels starting with improved sales and operations planning helps ensure the company has sufficient availability to meet the demand, reducing mother plant stress.
“From there, the continuous loop of information flowing from our customers to our farms and back again is critical to all of our success,” he said. “Finally, we never rest when it comes to the cleanliness of our farms and the material in them. Our dedicated scouting teams and on-site labs allow our farms to stay ahead of any potential challenge.”
Ball FloraPlant has also moved in the direction of on-site testing, according to Mike Klopmeyer.
“Many farms, including our Nicaragua farm, Las Limas, now have fully operational diagnostics labs, including the ability to sample and test on-site for critical plant pathogens like tobamoviruses,” he explained. “Early detection via monitoring at the farm can hopefully reduce the incidence of harmful viruses/viroids and bacteria in the cuttings shipped to our customers.”
New testing methods also add to increased diligence related to sanitation and disease prevention. At Vivero, Dennis explained changing a lot of routine virus testing from ELISA to PCR helps the company deliver disease-free young plants. In terms of pests, reducing dependence on chemicals, and instead looking to new biological approaches is necessary, he said.
“Our tendency is going towards the help of biological controls and more and finer screens, with the intention of leaving the bugs outside.
Over and above the cutting-edge technology mentioned above is always the people working with crops on a daily basis. Michel at Florensis knows this very well and explains their scouting team is armed with the latest knowledge and tools, including an app to monitor plants, pests and biologicals.
“Crucial to an effective IPM strategy is to have a strong scouting team. We believe that we have some of the best scouts out there,” he said. “But they do not work at night when many pests are most active. This is why we recently added PATS-C to our scouting team.”
PATS-C is an automated scanner that monitors airborne insects, even at night. This allows them to detect pests far earlier and easier, and react faster and more adequately to first pest pressure, he explained.
A new systems approach for clean plant production by USDA is another process improvement that should result in pest-free cuttings delivered fresh and on time, Mike Klopmeyer explained.
“The Offshore Greenhouse Certification Program (OGCP) controlled by the USDA, with annual facility inspections, allows farms to voluntarily enter a program,” he said. “Participants must meet certain clean plant production standards, allowing for better control at the source of the production for potential insects pests and diseases.”
Big wins
As if the improvements detailed above aren’t enough, the industry’s leading off-shore producers are quick to share other new processes and programs that have been implemented to optimize plant quality, improve working conditions or drive innovation. Above all else, they’re all quick to explain that these investments are made each year to level up the products that make up the backbone of the industry and help growers across North America achieve the highest standards.
At Dümmen, the company is working towards being more sustainable, lowering its CO2 footprint, reducing chemical and water use, and adding more MPS certifications.
“Working with live plants, our industry at every level faces routine and unforeseen pressures that can negatively affect our ability to deliver a quality product to our end consumers,” said Nathan. “But with [new innovations like] our Intrinsa breeding technology, we are focused on bringing new genetics to market that naturally reduce these pressures.”
“We are proud of Danziger’s new expansion into tropical foliage plants,” Mike Fernandez said. “This expansion will allow us to deliver clean tropical foliage items to the market that are grown inside and not subject to weather and disease issues like traditionally grown foliage.”
Danziger will use all the same techniques and protocols in place for annuals and perennials, with a focus on reliable weekly availability, he added.
Florensis is working hard to optimize mother stock production, as well as the rooting process, according to Michel.
“We made a big leap in this field with our vertical farming R&D climate room. Here, we can quickly change all climate conditions like temperature, humidity, light recipes—which include spectrum, intensity and hours of light,” he said. “This speeds up the process of fine-tuning the optimum conditions for our crops tremendously.”
Dennis feels a sense of pride and excitement with new opportunities to add crops and bring new innovations to a team of people intent on evolving and maturing.
“In recent years, we have increased the list of breeders whose varieties we supply. This has represented a challenge for all of us in our company, since adding new species means getting to know how to grow a different plant—some very different from what we are used to,” he said. “This helps us grow and evolve, and it makes me proud of being a part of this company. A company which employs hundreds of people and is trusted by many industry partners, distributors, breeders and growers in North America and other parts of the world.” GT