6/1/2021
Predicting the Future
Alex Fermon
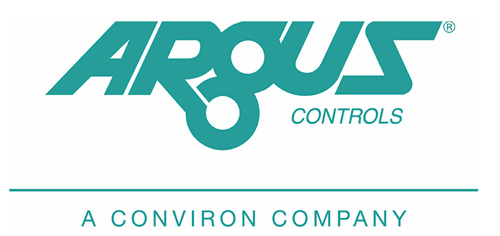
Fully integrated control systems allow growers to use any input as part of the control decision. In other words, you don’t have to wait for something to change—you can anticipate it and act immediately.
Pictured: Data collection is essential for decision making.
Waiting for a change to appear at the controlling sensor, such as a change in a zone’s climate temperature, is called “feedback” in engineering terms. Anticipating a change by observing known influences and acting preemptively is called “feed-forward.” As you’ll see, feed-forward control can be very helpful in efficient control of large greenhouse systems.
In effect, a feedback control system works in the past since an influence has already changed and then, some later time, the predictable effect shows up in the controlled space. A feed-forward control system works in the future since it reacts to environmental influences before they show up in the controlled space.
What is the value of integration?
Energy management: In large control systems, like those in greenhouses, using feedback alone can cause poor control and wasted energy. Using feed-forward, or integrated control, these problems can be avoided as preemptive changes can improve control and save energy. In addition, integration can also reduce wear-and-tear on equipment since it can reduce “hunting” and on/off cycles. In Table 1 are a few practical examples of the use of integrated controls in the greenhouse.
The hot water target for the mixing valve (violet line) is calculated using the heating setpoint, outdoor temperature, light level and the zone’s design. For this example, a water temperature target less than 120F was used to prevent overshooting, which can waste substantial amounts of energy. Instead, an appropriate target is selected and small changes are made based on feedback from the zone’s temperature sensor(s).
Table 2 shows three stages of unit heaters being controlled using integrated control. Notice how the stages are brought online progressively as the outdoor temperature (red line) falls. In addition, using pulse-width-modulation (PWM), the heater banks are turned on and off to maintain a nearly flat temperature line in the zone. This saves energy and improves product quality. Note that feed-forward changes are preemptive, whereas feedback changes can be 15 to 20 minutes later.
Data collection and archiving
One of the most valuable things you’ll get with a fully integrated control system is real-time data. Data collection and archiving are “built-in” from the drawing board. Some of the areas you can use data to get a return on your investment include:
• Better use of costly energy through improved control and accumulation of energy use, along with real-time weather information.
• Better project design, as the archived data could meet your demands without costly under-sizing over over-
sizing of the proposed systems.
• Overlaying data on real-time graphs helps you get to the root of problems quickly without costly “parts-changing” based on guesswork.
• Most non-integrated systems provide “snapshots” of control responses that won’t lead to solutions. In fact, in most cases, these momentary glimpses lead to disappointing troubleshooting results. In the worst case, snapshot data can mislead you, causing you to miss the real solution to a problem.
• Archived data available at your office computer can save hours of labor by bringing everything to you. You can review the environment your product was exposed to on a cold night in minutes. With a well-designed set of premade graphs and a “heating matrix,” you can find problems in minutes without leaving your office. Solutions can then be put in place to correct the issue before it affects product quality.
• Fertilizer and irrigation data can alert you to potential problems long before they can affect product quality or ship dates.
Remote access and control
Another great feature of a fully integrated control system is the ability to connect from virtually anywhere and being able to have complete access to your operation remotely. Most advanced systems send automated alarms informing of any issues and letting you know how serious the problem is. Some other advantages of having remote access to your system and being able to control it remotely include:
• Changing a setpoint without leaving your office or while you’re away from the greenhouse.
• Changing the way a certain piece of greenhouse equipment will be used, such as a shade curtain.
• Checking the performance of many different zones over the past day or days remotely at any time.
Pictured: Argus Live allows you to control an Argus system remotely and from any device.
ROI with integrated control
Converting or adding fully automated controls to your greenhouse could represent a considerable expense. Looking at the return on the investment will help justify the decision. It’s important to note that each operation will find more value in certain areas of the greenhouse than others and that the ROI (timewise) is different for each organization. Regardless of the uniqueness of every greenhouse operation, most integrated controls users will find improvement in the following areas:
• Improved quality control: Archived data lets you identify trouble spots and leads to effective solutions.
• Energy utilization and energy conservation: You may find that some energy conservation measures are hurting your product quality or extending crop turnover time. A small increase in energy input can be vastly offset by improved product quality or turn-around time.
• System troubleshooting: If you send a maintenance person to a trouble spot with no historical information, it could be costly. They’ll make their best judgment and replace a part, possibly a very expensive part. With reliable, real-time data, getting at a real solution is much easier.
• Project planning: Knowing exactly what’s needed helps to properly size the project to your needs. This saves money and other valuable resources.
Converting from local to integrated controls
Many greenhouse operations decide to move to integrated controls for many different reasons. Perhaps their operation has grown to a size that requires a more dynamic and integrated system, or maybe they’ve realized some processes might be more efficient using integrated controls. Usually, the controls company provides information and guidance on how to install the equipment, but key considerations are:
• Installing and wiring the weather station, zone climate sensors and other sensors, such as EC, pH, pressure transducers, etc. to the controller inputs per the manufacturer’s installation guide or direction.
• Interfacing the controller outputs to the controlled devices, which generally fall into two categories:
• On/off or digital devices, like fan stages, single-speed pumps, etc.
• Proportionally controlled devices (vents, curtains, etc.). These can be
• Networking the controllers to the computer access point. Typically, these networks are “hardwired” (such as RS-485) and/or Ethernet.
What to expect from integrated controls?
When choosing a fully integrated control system for your greenhouse operation, you can expect this to be translated into:
• Consistent, high-quality product season after season
• Energy implementation and conservation
• Water and fertilizer implementation and conservation
• Historical data for improved control, efficiency and year-after-year reference and project planning GT
This article was adapted from the GrowerTalks webinar “The Value of Fully Integrated Control Systems in the Greenhouse” presented by Jeff Woolsey and sponsored by Argus (March 25, 2021).
Alex Fermon is Product Marketing Manager for Argus.