11/1/2018
Doing More with Less
Ed Bloodnick & Troy Buechel
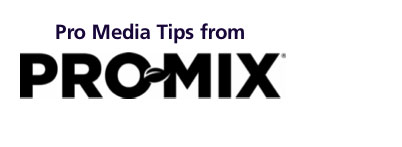
In the last year, the many state governments and municipalities have increased the minimum wage, resulting in higher labor costs. Over the years, it’s become increasingly difficult to find employees to work at greenhouses and nurseries. For team members currently employed, there’s also the consideration of increasing medical costs. All considered, growers and owners must find ways to improve efficiencies to reduce manual labor, attract new workers and minimize injuries to promote a happy, productive work force.
Identifying problem areas
Often we can be in the mindset of “this is the way we’ve always done this.” Change isn’t always easy, but it first starts with an understanding that there may be a better way to do something and you need a commitment to make a change.
To improve efficiencies, you need to identify the problem area(s) that are at your operation. Team members are the best source to identify problem areas and possible ways to improve efficiencies. Team members work every day at the same job, so it makes sense to consult with them for their input.
Pictured: Example of a transplant line that minimizes team member fatigue. Floor mats and stools reduce leg and back fatigue.
There are different ways to do this—you can have a drop box for team members to put in anonymous notes or have a “pizza meeting” to encourage discussion with team members. Another effective method is to offer an incentive for “best ideas.” This can be a simple cash incentive or offer a day off to a team member with a great idea.
What’s an improved efficiency?
Any improved efficiency should take into account: 1) automation of a process(es); 2) promote a safe work environment; and 3) reduce repetitive strain injury. The goal is to work smarter—more efficiently—reduce risk of injury and improve productivity.
For example, a transplanting line can be tedious and tiring for transplanting small seedlings. The addition of cushion floor mats on concrete floors reduces leg and back fatigue. If possible, stools or elevated chairs allow team members the choice of standing or sitting to reduce fatigue.
Repetitive strain injury (RSI) occurs from the prolonged performance of repetitive actions, forceful exertions, vibrations, mechanical compression, or sustained or awkward positions, typically with the hands. This can cause pain or impairment of function of the muscles, nerves and tendons. Injuries can occur for office team members working on a computer or team members working in the greenhouse.
There are no quick fixes for RSI, but prevention is worth a pound of cure. Light exercise equipment and stretching exercises help to reduce RSI and can be part of the break routine for team members.
Growing media handling
In the case of potting media, it’s typically packaged in bulky, heavy packaging that’s awkward to handle from the moment it’s delivered to the day the package is opened and used. Peat-bark mixes are always packaged in loose-fill bags, since compressing bark results in a very heavy packaging.
Peat-based growing media are available in loose-fill bags (2.8 and 80 cu. ft.) or compressed package sizes (3.8, 55 and large-format mega-bales). Loose-fill packaging is best for convenience of use, since product doesn’t have to be decompressed, but 2.8 cu. ft. bags can cause back strain from lifting and larger formats still require more product handling.
For compressed bales, the cost per cubic foot of growing medium is typically a little bit less. This is because the cost of the freight is offset by the compressed volume, since twice the volume is delivered in a truck. However, small compressed bales are heavier and may be too heavy for some workers and can cause back strain.
Large mega-bales are a format to consider to gain efficiencies and reduce worker injuries; however, purchase of a bale breaker is required to decompress the large-format packaging. A common objection to switching to large-format packaging is the up-front cost of purchasing a bale breaker.
When considering many factors, automation improves efficiencies. Depending on your actual annual usage, the return on investment could occur surprisingly fast.
Below is an example of the cost savings when switching from a full truckload of one package size (first column) to the large-format 135 compressed packaging. The savings is based on the number of equivalent cubic feet in one truckload of the current package size compared to the same number of cubic feet provided by the large format.
For a greenhouse that uses five truckloads of the 2.8 cu. ft. loose-fill bags, there’s a savings of close to $20K in the first year. Considering a large bale breaker can cost between $18K to $26K, the return on investment could be in less than two years.
Reduced cost of procurement isn’t the only advantage of switching to large-format compressed packaging. Other advantages include less disposal of waste, reduced employee handling and reduce exposure to team member injuries. Here are some examples:
• Less waste: 15% to 18% less plastic packaging to dispose, no shrink-wrap and fewer pallets to dispose
• Reduced storage space needed. As mentioned in the chart, 22 pallets of loose-fill products is equal to 14 pallets of a large-format 135 cu. ft. mega-bale and 22 pallets of the 3.8 cu. ft. compressed bales is equivalent to 18.5 large-format 135 compressed packaging
• Less employee handling: One bale is placed into the bale breaker vs. 57, 2.8 cu. ft. bags or 30, 3.8 cu. ft. compressed bales.
• Less labor: Only one person is needed to place a large format bale into a bale breaker vs. two people having to place many smaller package sizes into the hopper of a bale breaker/flat filler
• Reduce back injuries: All movement of the large-format bales is done by forklift. There’s no hand-lifting of bags or small bales into equipment.
Improving efficiencies at your greenhouse can be a holistic approach, from consulting with employees, visiting other grower operations, attending trade shows for new ideas/and equipment, or looking at other businesses outside of the horticulture industry. Not all improvements are attached to significant costs—sometimes simple measures and common sense prove to be the most effective for a more productive and safe work environment. GT
Ed Bloodnick is Director of Grower Services and Troy Buechel is Horticulture Specialist—Mid-Atlantic U.S. for Premier Tech Horticulture.