10/28/2016
Internal Transport Devices in a Lean Flow World
Gary Cortéz
In the lean flow world, one of the key tenets is the elimination of waste (“Muda” in Japanese). Waste is also defined as non-value added—anything that adds cost to the product, but doesn’t increase the worth of the product.
There are seven elements of waste that are targets for elimination. One of the seven is transport or transportation. When a product is being moved, are you adding any value to it? No, if anything we’re adding cost to the product. These costs come from labor used to move it, equipment required to move it, as well as possible damage to the product. Unfortunately, we have to move our products in our greenhouses and nurseries.
Pictured: Moveable/rolling benches (or Dutch trays) move a lot of product quickly. Many growers, like Van Belle Nursery in British Columbia, use them. Photo courtesy of Van Belle Nursery.
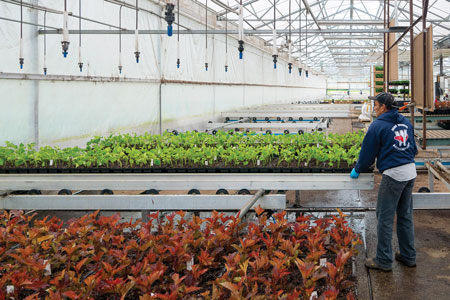
So the question becomes: What’s the most efficient way of moving the product? We’ve worked with many growers and have seen just about every possible transportation device that’s been developed. Below are some of the options growers use.
The shelved rack
The shelved rack is probably the most common carrier that we’ve seen. There are many versions of the rack—most are metal, some are rectangular, some are square, some have fixed shelves and some have adjustable shelves. These racks are great for moving product through the greenhouse and in some nurseries. They work great when the ground is concreted or paved; they don’t work very well in uneven surfaces.
Some of these racks can be “trained” (linked), where many growers will have three to as many as 10 racks trained together. The rectangular racks, also referred to as CC, Danish or Dutch racks, are easier to move around since they’re lighter than the square ones and about half the size. However, since they’re smaller, they hold fewer plants.
The square racks, also known as Cannon or Wellmaster racks, hold more product, yet they’re more difficult to move around and are only accessible from one side. Many of our customers use the square racks in our shipping supermarket design to store product. They then “shop” the supermarket with the rectangular racks.
The racks with the adjustable shelves work best when it comes to optimization of space. Since you can adjust the shelves based on the plant height, the variables are endless. The fixed shelves tend to have a lot more air (space between the shelves) because not all plants match the predetermined shelf spacing. In either case, the metal racks seem to be the most versatile carrier and work well with our lean processes.
Conveyor belts, rollers
Those of you who’ve followed FlowVision and have heard us speak or read some of our articles know that we’re not big fans of people working on belt conveyors. Belt conveyors are meant to convey product. But, with that being said, we use belt conveyors when it makes sense.
If we put a product on a belt conveyor and it travels a couple hundred feet, that’s labor that we’re saving by not having to have a person move the product. It becomes an issue if an employee is waiting for the product to come to them on the conveyor. This wait time is considered to be waste. So which is better—do we wait or do we physically move the product? The answer is: Which one takes less time?
We’ve seen many growers use portable belt conveyors or roller conveyors to lay down or pull product in hoop houses or fields. The problem with this is that it takes a long time to set up and take down the conveyors. We were recently at a nursery in North Carolina and they were using portable belt conveyors to lay product down. We did a quick analysis and determined that by the time they set up and tore down the conveyor they could have laid down product in one-fourth of the hoophouse compared to doing it by hand. The decision from this analysis was not to use the conveyors anymore and look at wheeled carts as an alternative. The wheeled cart requires no setup time and the employees are able to carry more product.
Wheeled cart
Wheeled carts with pneumatic wheels work well in places where a rolling rack can’t be used. The grower from North Carolina replaced the conveyor with wheeled carts. It’s less tiring for the employees, and the laydown and pulling is done much quicker. The wheeled carts are great when there’s limited space for a rack or the ground isn’t smooth. There are many versions of wheeled carts that work well—a two-wheel or four-wheel, a single shelf or multiple shelves. The one that works best is the one that fits the requirements of the grower.
Overhead monorails
Overhead monorails work well in houses where carts cannot go down the bays or carts are too tall. We’ve seen many of these monorails with multiple shelves move product in and out of houses very efficiently. The optimal design for these monorails is to have a system where you have a two-way flow. This means that you can send the monorail down a bay and then loop it back on another rail. This allows for better flow and is usually more efficient.
A down side to monorails is the design. Monorails need a rail to ride on, which becomes an issue for some growers. In some cases, the houses can’t support the weight of the carts or it’s too expensive to put in the infrastructure to be able to use them.
Moveable (Dutch tray) benches
Another commonly used transportation method is the moveable/rolling benches. This method moves a lot of product quickly. If a grower can create a flow of these benches where they come in from one end of the row or bay, and are pulled from the other end in a first in, first out basis, then they work great. The issue is when this method isn’t possible. It sometimes seems that you need product from a bench that’s in the middle of a row. If you don’t have a crane or elevator to get to the bench, you need to move the benches in front of the one you want and then move them back. This creates additional waste.
Another consideration is the cost of the benches and infrastructure compared to racks. We’ve done studies on benches compared to racks and have found that in the same floor space of a bench you can fit between two-and-a-half to three times the amount of product. This is something to consider if you want to use your benches to stage product.
We have many customers who have these benches and they love them. Again, it needs to fit your specific requirements. Dave Van Belle, president of Van Belle Nursery in British Columbia, stated, “The benches allow us to improve our production efficiency, especially when it comes to time-sensitive, labor-intensive tasks. For example, when crops are rooted during propagation, crops can easily be moved out of the house and replaced with new crops within a couple hours, using only a couple people. Easy movement of plants allows us to keep our houses full with minimal people required.”
Forklift pot spacers
Another option to efficiently move product to and from houses is a forklift with pot spacer forks. There are several manufacturers that offer this type of carrier. They work well for growers that are higher volume and have the space in their greenhouses or hoophouses where a fork lift can easily get in and out. They require wider aisles and the ability to get the forklift into the bay.
It can do the work that would normally take several people to do, thus being more efficient. The true test to see if it makes sense for a grower is to ask: do you have the space and room to be able to maneuver through the houses? If you do have the space, then you need to compare the cost of the way you currently do it versus the pot spacers. Not every grower is going to come to the same conclusion.
As you can see from the numerous examples detailed in this article, there are many ways of reducing your waste or non-value added work. Some of them require infrastructure or electrical power. Some of them are simple and cost effective. The common theme in all of the options shown above is twofold. First, all of the transportation devices discussed above are all geared toward improving the efficiency of the employee and reducing the walk times. Second, and probably most important, a device that works for one facility may not work for another. Understanding the facility restrictions and opportunities will help in making the right decision as to which device will perform best to achieve the most productivity benefits.
GT
Gerson “Gary” Cortés is a Partner at FlowVision—a Colorado-based Lean Flow Consulting Company. He’s been implementing Lean Flow since 1986 across many industries around the world. He can be reached at Cortes@flowvision.com or (561) 301-8740.