10/28/2016
Wood Works as a Peat Option
Dr. Brian E. Jackson
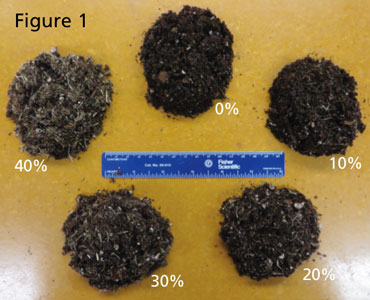
For decades, we’ve relied on peat moss as the primary substrate component to grow most greenhouse crops. Peat moss is undoubtedly an ideal material based on its excellent physical and chemical properties. Research on substrates continues today as vigorously as ever (maybe even more so), despite the successes and familiarity of our traditional peat-based mixes.
There are several reasons why there’s a continued interest by some to develop new substrates and substrate components. First, greenhouse crop production has changed over the decades and so has the need for more specialized and uniquely designed substrates to meet the needs of new crops (orchids and cannabis to name a couple) and cropping systems, new irrigation technology and increasing pressure on water use and management. Peat is still good for these changing needs, but so is the potential for other materials.
Secondly, there can be occasional peat shortages associated with wet seasonal harvests from the peat bogs in Canada, which may be the case to some extent looking forward to 2017 based on the recently announced possible peat supply concerns (lower-than-expected harvests in 2016) that have been reported from the Canadian Sphagnum Peat Moss Association.
Thirdly, the cost of shipping peat moss from Canada throughout the U.S. is something that many people want to reduce by finding alterative materials that are regionally specific to different areas of the country. What should be noted is that the continued search for “new substrate materials” isn’t due to a lack of peat or because of improper peat harvesting that would cause environmental concerns. The peat producers in Canada do a marvelous job of managing, harvesting and replenishing their peatlands. Wet summers and high transportation costs are the culprits that have caused peat-related substrate issues in the past.
Wood as an alte
rnative
Over the decades, as many alternative materials (likely hundreds) have been investigated to some extent, none have shown the potential like that of wood-based materials. A close look at the number of scientific papers and abstracts, popular press articles, education/trade show talks, and research conference proceedings over the last 12 years indicates that wood-based substrates and substrate components by far show the most potential as a peat extender or alternative.
“Extender” or “alternative” are better descriptors than “peat replacement” for the simple fact that peat cannot be “replaced.” The use of fresh wood components in substrates started in the late 1980s in Europe, but only made its way here to the U.S. in 2004. Since the 1980s, there have been many commercial wood fiber products available to European growers, a trend that continues today. Some former and current products like Hortifiber, Toresa, Fibralur, Greenfibre, Forest Gold, Culti-Fibre, Pietal, Torbella, Fibrosana and Ekofiber have been used to some extent across much of Europe. Fast forward to 2016 and there remains large-scale production and commercialization of wood fiber by some of the largest substrate companies in Europe, including Pindstrup and Klasmann, among others.
In the U.S., there’s been a tremendous amount of effort, resources, investments and energies spent on the development and trialing of wood substrates and substrate components in the past 12 years. Evaluations have been conducted by academic researchers at numerous universities, substrate manufactures, private entrepreneurs and independent growers. Early work focused on figuring out how to grow crops in 100% wood, while current efforts are centered on using wood materials as an amendment to peat moss in the range of 10% to 40% (Figure 1).
Does wood work?
At the Horticultural Substrates Laboratory here at North Carolina State University, we see many wood substrate materials pass through our lab and we ourselves have a vigorous research program focused solely on this “wood substrate initiative” (Figure 2).
During trials that have been conducted over the past eight years, there have been more successes than failures and more opportunities with using wood than any other non-peat material. As with any new material, there are nuances that must be identified, understood and worked out before commercialization and grower acceptance can occur.
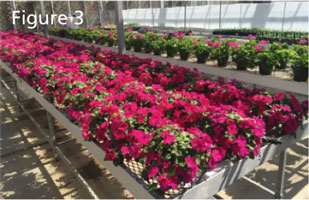
Trials have been conducted on dozens of species (flower and vegetable) in different container sizes and configurations, under various irrigation regimes, fertigation regimes, etc. (Figure 3). One of the most widely reported, and at this point well-accepted, observations relates to the accelerated root growth in many crops (Figure 4). Maximum root growth isn’t always a good thing for many crops during certain stages of production, as it can change irrigation needs and help accelerate plant growth more than needed sometimes. However, when considering the potential benefits of quick rooting of plugs, bedding plant flats, difficult-to-root species, etc., there could be some advantages.
Research on wood substrate components has indeed made great strides towards better understanding how and to what extent these materials can be used with or without peat. A decade ago, it was common practice to just “grind up trees” and try to get the resulting wood product to grow plants. Not anymore! Work has now evolved to be very focused to answer v
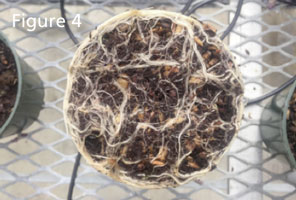
ery specific questions, solve specific problems and explore new opportunities relating to the use of wood components.
We here at NC State University are leading an international coalition of scientists and industry leaders across North America and Europe to comprehensively address many of the still unanswered questions and concerns of wood substrates. Our current research and development on nearly two dozen wood substrate materials include:
- Engineering practices that are looking at the different types of machinery used to make wood components and the many variables associated with making consistent, reproducible and reliable products on a commercial level.
- Characterizing the many different wood components that are being made by assessing particle shape and size, surface area and degradation rates.
- Physical and hydrological properties of wood components and substrate blends containing wood, which include total porosity, air space, water-holding capacity, bulk density, wettability, hydrophobicity, initial hydration, available and unavailable water, water flow and drainage, packing, settling, etc.
- Chemical properties including pH, pH buffering capacity, cation and anion exchange capacities, phytochemical toxicities, PGR efficacy and tie-up, etc.
- Biological properties, including microbial populations, nutrient tie-up (nitrogen and sulfur), degradation and shrinkage rates, pest and disease interactions, etc.
The where and how of wood substrates
Research has shown that in the U.S., loblolly pine (
Pinus taeda) is the best tree species for making wood substrates. This has been proven after investigating dozens of tree species over the years and evaluating the performance of crops grown in them. Other species of pine have been used successfully, but none are as plentiful as loblolly. Loblolly pine is a native species and is the most cultivated (by acreage) in the Southeastern U.S., which makes it a plentiful resource.

Spruce (
Picea), fir (
Abies) and larch (
Larix) species have also been shown to be viable options. Other competing uses of pine (lumber, pulp and paper, wood pellets, other wood-derived products, etc.) don’t seem to be of concern due to the millions of acres of trees being grown.
There are many different machines used to initially grind/shred harvested tree logs into a smaller material that can then be further processed in other machinery to create a desirable substrate component. The method by which trees are initially ground can create wood materials that when further processed yield very different products.
Understanding these differences and variables is not only important in producing consistent materials, but it’s also key in our current understanding of how to actually create very specific wood components that can be used in different ways. For example, if a tree is harvested and processed in chippers, the resulting wood chips can be made into wood aggregates as a perlite alternative/replacement material. These wood chip aggregates have been thoroughly researched and results published highlighting their use as substitute to perlite in greenhouse mixes without any effect/change in physical properties, nitrogen needs, liming adjustments, PGR tie-up or disease susceptibility. These chips can also be colored/dyed if desired.
The three main types of machinery used to process wood chips/shreddings are hammer mills, extruders and disc refiners. Each of these machines will generate very different wood materials that can have different uses and functions when blended into a substrate mix. Understanding that all wood products/components are NOT the same is going to be very important for substrate manufacturers and growers to realize and understand.
Commercialization of wood fiber in the U.S. has made a lot of progress in the past two to three years, with several wood fiber components currently on the market. Products including HydraFiber (Profile), Forest Gold (Pindstrup) and Greenfibre (Klasmann) are currently being marketed/sold as are other specialty blends offered by Oldcastle and Berger Peat, to name a few. Some of these wood fiber products are compressed into bales similar to peat moss or coconut coir (Figure 5) that require special equipment and handling to properly fluff/reconstitute them before being blended with peat or other materials to create a growing mix. Other materials, primarily those made in hammer mills, don’t require special equipment for fluffing or blending. These questions should be asked before investments are made into the use of these new materials.
Before you add wood
Other than blending differences, there are some other factors that should be considered by growers when using substrates that contain wood fiber. First, high pH during crop production can be an issue if liming rates aren’t adjusted (lowered) to account for the wood fiber additions (and loss of a percentage of peat moss). Wood fiber has an inherently higher pH than peat moss and, therefore, when higher percentages are added to a mix, the result is a higher pH, which can be further raised by “normal” lime amendment rates.
Secondly, when wood fiber is blended with peat moss, it creates a very unique “matrix” resulting from the fiber of the wood and peat locking/nesting together to form somewhat of a spongy-feeling substrate. This can be very good for overhead irrigation applications, as there’s no splashing or channeling that can often occur in a peat-lite (peat/perlite) substrate. The wood fiber can also help wick water easily from sub-irrigated systems and move the water higher/thoroughly in the container.
The wood fiber increases substrate wettability and water capture better than peat alone or peat amended with perlite. The wood fiber will often dry out on the surface quicker than peat, so special attention to watering is needed so as to not overwater crops based on what the surface of the substrate looks like. The dynamics of the peat and wood fiber (depending on percentage used) can increase the drainage of substrates and may require less water at each irrigation, but more frequent irrigation applications. This, of course, is crop and container size dependent.
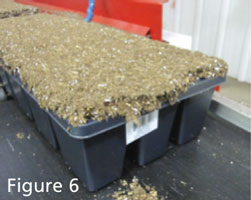
Lastly, it’s of interest how automated pot-/flat-filling machines and plug transplanters will perform in peat mixes containing wood fiber, given the different texture of the mix (Figure 6). If the percentage of wood fiber is too high, there could be complications in getting certain sized containers properly filled or getting plugs to insert into the mix as expected. If these issues occur, modifications to the system or to the process may have to be made to ensure proper planting.
Much remains to be learned about using wood components in our substrates, but the perceived advantages and potential is believed by many to be well worth their investigation and consideration. Work continues at NC State University in the Horticultural Substrates Laboratory and at the Substrate Processing and Research Center (SPARC)—which was constructed in 2014—to better investigate the engineering and utilization of wood, bark and other organic substrate components.
Wood substrate research will also be on full display and thoroughly discussed as one of the main topics at the International Symposium on Growing Media, Soilless Cultivation and Compost Utilization event, which will be held in Portland Oregon, August 20-25, 2017. This symposium is part of the International Society for Horticultural Science and will focus on all aspects of growing media and soilless cultivation. It welcomes all substrate research scientists, growers and industry professionals from around the world.
GT
Dr. Brian E. Jackson is an Associate Professor and co-director of the Horticultural Substrates Laboratory in the Department of Horticultural Science at North Carolina State University. Brian can be reached at Brian_Jackson@ncsu.edu.