5/27/2016
Robot Sticking is Here
Chris Beytes
We have found the holy grail. It’s located in Huntersville, North Carolina, in the southwest corner of the downstairs production area at Metrolina Greenhouses.
No, not THAT Holy Grail. Horticulture’s holy grail—the automated cutting sticker. Designed by robotics manufacturer ISO Group, Metrolina’s newest piece of greenhouse automation, the ISO Cutting Planter 2500, is the first machine* to dependably stick a wide variety of unrooted cuttings—and not just the easy, woody stuff like chrysanthemums, which have been stuck automatically for years. We’re talking calibrachoa, verbena, bacopa—even lysimachia—and at an average rate of 2,000 cuttings per hour (2.5 times faster than Metrolina’s average human sticker).
We visited Metrolina in March to see it in action for ourselves and get the details from brothers and co-owners Abe, Art and Thomas Van Wingerden. (Brother Michael was busy in the greenhouse testing yet another Metrolina innovation: an inventory system that will let five people count 30 acres of finished production in just four hours. But that’s another story.)
Metrolina’s need to stick
When you hear a few statistics about Metrolina circa 2016, you can see how robotic cutting sticking might be desirable. For instance:
- Size of greenhouse: 170 acres
- Number of employees at peak: 1,100
- Number of cuttings stuck per week during 12 peak planting weeks: 1.8 million to 2.1 million
- Number of semi-trailer loads of finished product shipped on a busy spring day: 130 to 160
- Sales: Approaching $200 million
Any wonder they want to automate the sticking process?
Pioneers in greenhouse automation, the Van Wingerdens have been looking for a way to stick unrooted cuttings automatically for years, and most seriously for the last three or four years, as computer and camera technology have made the idea more practical.
More than a decade ago, Dutch chrysanthemum producer Dekker Chrysanten pioneered robot technology to stick mum cuttings; these, however, require special cartridges to be loaded with cuttings at the offshore facility—meaning a human is still sticking the cutting, albeit in a lower-cost country.
More recently, mum competitor Deliflor followed suit, but using true robots built by the aforementioned ISO Group. These can actually pick up and stick loose cuttings dumped from bags onto a conveyor belt. Deliflor now has 30 machines in operation, transplanting some 2 million mum cuttings per day. It was seeing these robots that inspired Sim McMurry, Metrolina’s Director of Product Development.
“He came home on fire,” recalls Art. “He told me and Thomas, ‘You guys have gotta go over there!’”
Thomas joked that Sim is always getting excited over the latest gizmo, but after about three months of inaction from the brothers, he got insistent, so they visited Deliflor. “We were duly impressed,” Art admits.
They wasted no time in meeting with ISO Group to discuss Metrolina’s needs.
“We told the guys from ISO that if you can stick calibrachoa, verbena and bacopa—small cuttings that are not as woody as the mums that [Deliflor] is sticking—we’re interested.”
This was 2013. ISO Group spent the next two years developing the new robot, with Art and Thomas making half a dozen trips to the Netherlands to see how it was working. But two years was long enough.
“We went over there in November and basically told them, ‘You have to ship it!’” says Art. “They said, ‘It’s not running 100% yet.’ We were like, ‘We don’t care. You have to ship it. We want it NOW! Ship it now!’”
Abe explains: “We’ve learned from all of our other technology and innovation around here that we don’t need it at 100%. We need it at 80% because we’re going to give you the last 20%.”
That was unsettling to the perfectionist Dutch engineers, but they obliged. Metrolina took delivery of the new robot in January.
How it works
ISO Group uses an off-the-shelf Denso four-axis industrial robot and computer (used for thousands of different applications around the world) to handle the movement of the cuttings, then developed a gripper appropriate to picking up a tiny cutting.
Two cameras above the machine’s conveyor belt take snapshots of the cuttings, looking specifically for the bare end of the stem. The computer relays the location and orientation information to the arm and gripper, which then picks up, transports and sticks the cutting into a waiting tray. The whole cycle takes less than two seconds. When the cameras can’t spot any more stem ends, it gives the conveyor belt a jostle, which tosses the cuttings into the air, freeing up more visible stems.
All the worker has to do is make sure the machine is supplied with cuttings and empty trays. Oh, and fix the occasional miss because no machine is perfect. But it’s a constant and consistent process, with little drama. On average, the robot can stick upwards of 2,500 cuttings per hour, according to ISO Group’s website; Metrolina’s average of 2,000 is more conservative and real-world, taking into account downtime and changeovers.
“We’ve gotten 2,200, 2,300 on some stuff,” says Art, “but 2,000 is what we’re shooting for.” In comparison, 800 per hour is their overall average for sticking by hand.
Accuracy is “very good,” says Art. “It hits the center of the cell, it sticks it to the same depth.” That’s most critical to how well and consistently a tray of cuttings roots, explains Thomas. “A person doesn’t have good depth perception when they’re sticking a cutting in soil.” With the robot, the depth is the same every time. “If you set it at a half inch, it’s a half inch. That makes it root out quicker in the greenhouse.”
How a robot could change your cuttings
One key to the robot’s ability to work efficiently is the cutting itself. It needs a clearly visible stem that’s long enough to easily grab. But cutting specs can vary, with some stems longer than others, and the occasional leaf at the end of the stem that has to be removed by a worker.
Says Art, “That’s something we’ve got to work on with the cutting guys. They’ve all been here, they’ve all seen it runnin' and they all want to get better.” Abe added that all the big cutting
producers have seen the sticker in action, are impressed and say they’re open to the idea of adjusting their cutting spec. The best part is a cutting that’s better for the robot is easier for a human to stick, too, says Art. It could become the new industry standard.
By the time we saw the machine in action, it had been going through its paces at Metrolina for several months. Any problems or issues so far?
“We don’t have enough of them,” quipped Thomas.
Abe agrees. “It’s doing what we thought it was going to do. Our biggest issue right now is cutting spec—making sure we get the spec of the cutting to what we need.”
Art added the cutting handling is also important. The calibrachoa cuttings we were watching go through the machine were a bit limp, which led to some misses. Art says they need to be fresh and turgid, ideally out of the cooler for no more than 10 minutes before sticking. They also use talcum powder on the cuttings to keep them from sticking together. Tray fill consistency is important, but no more so than for hand sticking. And the tray fill is the same.
Crunching the numbers
What are the economics of automated sticking? Art has calculated the numbers for Metrolina thusly:
The average person sticks 800 cuttings per hour. Metrolina’s average labor cost is $20 per hour by the time you count in everything. That’s 2.5 cents of labor to stick a cutting. With five machines doing 10,000 cuttings per hour (their goal by November 2016), with five people to manage those five machines, that’s $100 per hour of labor or 1 cent per cutting—a savings of 1.5 cents per cutting. And that’s just labor cost. Labor availability is an even bigger factor.
“Every greenhouse we visit has trouble [finding] labor,” Art says. “If you can’t get the labor, then you have to automate. So it’s a penny and a half savings every time we stick a cutting and we don’t have to hire somebody to do it.”
Art mentioned five machines doing 10,000 cuttings per hour. That’s enough for half their demand during the 12 busiest weeks of the year and all their demand for the other 18 weeks of heavy sticking.
“We will never stick all 2 million cuttings per week with a machine,” says Art. It would be too much capacity left idle for much of the year, which is why they’ll always depend upon skilled humans to stick cuttings.
Abe wanted to emphasize that they are not out to eliminate employees. In fact, the folks sticking cuttings by hand know the robot is working away in the next room, but they’re not worried about it taking away their job. In fact, automation can lead to higher-paying jobs. Says Art, “Somebody who can run a machine can earn $15 to $18 an hour to do it.”
The late Tom Van Wingerden was famous for preaching “automate or stagnate.” Looks like his sons won’t be stagnating anytime soon.
*Metrolina’s is not the only ISO Group robot in the field. Dutch grower Bennie Kuipers, whom we’ve written about several times in the past, has an array of five similar ISO Group sticking machines working at his Emsflower facility in Western Germany.
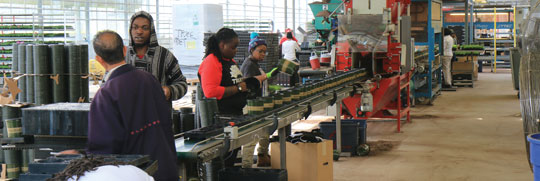
When Long Lines Are Good
During our Metrolina visit, Abe pointed out a change they’ve made to all their planting lines: They’re now longer by roughly 60 ft. Why? Production Manager Art explains:
“Two years ago, Thomas and I saw that our [production] numbers weren’t as good as they used to be. Well, we do a lot more combos now, a lot more decorative pots, bigger baskets, things like this. So what ends up happening, we try to put seven plants in a combo. You and I are on top of each other. You’re putting yours in, I’m putting mine in and I hope I’m catching up. And somebody else has to put a hanger on it while it’s flying down the line.
The solution was to put a 90-degree turn in the line and add 60 ft. of conveyor. That gives everyone more elbow room to work and more buffer for flats and pots, meaning fewer stops of the line.
The result has been so positive, they had to have their pot fillers modified to work faster—they were maxing them out. Now workers are doing more and doing it more comfortably.
Think about that next time you consider cramming more into the same space. GT