10/28/2015
Eight Weeks. 3.5 Million Cuttings. One Machine.
Steve Corcoran
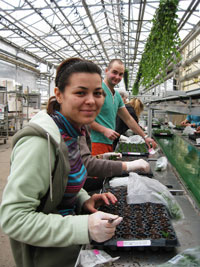
It’s not one of the most sought-after tasks, but it’s certainly one of the most vital in terms of a greenhouse’s future earnings. Transplanting cuttings to flats—or sticking—is traditionally one of the most time-consuming, labor-intensive jobs that workers are begrudgingly assigned to.
But if the task was made simpler through an automated process that offers a comfortable workstation that simplifies the work, would workers respond in a more positive light? And would output improve?
Last year, Bergen’s Greenhouses put that notion to the test. The Minnesota-based greenhouse grower—which specializes in perennials, holiday plants, plug and liner material, garden mums and bedding plants—made the switch from its Dutch tables to an automated sticking line from AgriNomix and has since realized a 30% increase in worker productivity and overall output.
Pictured: Automated sticking lines offer increased ergonomics and are configured to just the right height, so workers can stand if they choose or sit comfortably on a stool to do their work.
Starting with a long-term business outlook
Investing capital to improve an existing production process that’s been in place for generations certainly involves some thought. But if the result is increased efficiency, then “fixing what’s not broken” is a decision that must be made to remain viable in such a competitive industry, admits Chris Bergen, who along with Kevin Johnson, co-owns and manages Bergen’s Greenhouses.
“We’ve always been very forward thinking,” said Chris. “This is something my father really tried to impress upon Kevin and me, and it’s just as important today as it has ever been. Efficiency is the key to longevity in this business and we’ve invested heavily in our facility because we firmly believe that today’s equipment offers the best chance for efficiency and low-cost production.”
Those key automation attributes are important from a business sense, but they also represent how greenhouses are adapting to ever-changing markets, according to Chris.
“Today’s market reflects the changing times. There’s been a decrease in customers investing their time in gardening, but a growing market for customers who appreciate the ready-beauty in items like patio boxes,” he points out.
Bergen’s Greenhouses has recognized and adapted to that changing market and it’s certainly paid off. By switching their product offerings from small pots to retail-ready products, they’ve managed to grow that niche tenfold.
“Not many years ago, we were producing 25,000 patio pots. Now we’re doing 250,000 patio pots,” Chris said. “That’s a big swing in a short amount of time.”
According to Chris, the sudden increase in the company’s retail-ready product line has naturally created a similar demand in production output.
“We’re doing about 3.5 million cuttings in an eight-week period, so we naturally were looking for easier ways to perform this function,” he says. “We used to use Dutch tables and brought the work in via rolling containerized tables, but the employees really didn’t like working on the tables.”
An offer they couldn't refuse
An AgriNomix rep visiting the operation pointed out to Chris how inefficient the sticking process was, but he didn’t bite.
“I kept procrastinating until the rep finally offered to set up a trial sticking line, saying we could send it back if we didn’t like it,” Chris explained. “We were only two weeks into the trial when I called him to say, ‘Send the bill, we’ll keep it.’”
The simple advantages that an automated sticking line has over a static operation is that the system literally brings the work directly to the worker, which makes the task easier.
“It’s just a better way of handling material with less moving parts,” said Chris. “Everyone is comfortable. Trays are dibbled when they reach the worker and then move right to watering. People enjoy this process more and we see increased output per hour, per day. It just leads to more organized work.”
How you work = How fast you work
Because an automated sticking line offers increased ergonomics and is configured to just the right height, workers can stand if they choose or sit comfortably on a stool to do their work. All the material is directly in front of them and, more importantly, the work comes to them, which is a key component to production efficiency.
“The AgriNomix tech flew in to make sure everything was right with set-up,” Chris said. “They set the sticking line up in one day and the next day we went to work on the equipment. After just the first few hours of running, we realized we had a good thing.
“Our output is amazing now. We’re 30% more productive using the same amount of people working across all genuses. We can run six to eight products simultaneously on this sticking line. Each individual worker can be doing something different at their station. They just stick, tag and send the tray to a person down the line who sorts the different products. We can do multiple products and small runs very efficiently now.”
Chris says it’s that flexibility that offers the most benefits for his operation.
“What got us was that we could do a tremendous volume of cuttings in a day,” he noted. “We needed to do more work in less time, and previously, we would split up crews to work separate varieties. Now we have one crew working the line with a wide mix of products.”
GT
Steve Corcoran is CEO of Look Strategies, a marketing communications firm reporting on advancements in the horticulture industry.