10/26/2012
Step Saver
Chris Beytes
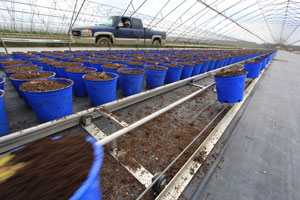
Centerton Nursery’s 600-ft.-long greenhouses are made a lot more accessible, thanks to this unique nursery-designed cable conveyor.
Centerton, in Bridgeton, New Jersey, has 120 of the giant houses to fill multiple times per season. Rather than fill and plant in a production barn and trailer the pots to the houses, they long ago decided the most efficient way was to bring the potting machine to the houses. So they mounted a pot filler on a tractor-pulled trailer.
But getting the filled pots into the 600-ft.-long houses was the next challenge, and a conveyor proved to be the answer. Business founder Ray Blew designed the first one in 1988, says his grandson, Donald.
“It was a huge, massive conveyor with a 5 hp electric motor,” he recalls. Four prototypes and many years later, and today’s version easily moves 70 1-gal. pots a minute or 45 2-gal. pots a minute with just a 1 hp motor.
The design is elegant in its simplicity. A single steel cable suspended on pulleys runs in a loop. Pots sit on the cable and lean inward slightly, sliding along an aluminum tube. Workers grab pots as they reach the desired point in the greenhouse.
Each house is equipped with its own aluminum conveyor frame, but to keep costs down, the drive unit (inset) and cable is moved from house to house. Workers can set up the motor and 1,200-ft. cable in about ten minutes, says production manager Joe Blandino.
Donald says they fill, plant and space from 8,000 to 20,000 pots per day. He calculates that the conveyor increased production by 23% per man hour compared with parking the potting machine alongside the houses and having to reposition it several times a day, which is how they did it before the conveyor.
“They work very well for us because we already have the means to pot, trim and so forth at the house instead of in a potting barn like most growers,” says Donald. “It has taken us about five years to implement them totally, to spread out the cost of building and installing the conveyors.” GT