2/21/2012
On Trend
Jennifer Zurko
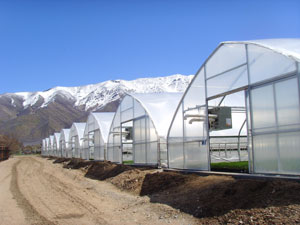
We know what you’re thinking: How could anyone afford/have time/want to build new greenhouses right now? But guess what? Some of you are.
Golden Pacific Structures offers the Windjammer series 5000 stand-alone cold frames, which are ideal for a wide range of growers, both large and small.
During the last two years, grower visits have included tours through their construction sites or new facilities. Ivy Acres on Long Island, Rosa Flora in Ontario, Lucas Greenhouses in New Jersey, and Grower Direct and Cromwell Growers in Connecticut, are a just a few that were in the process of or just finishing up new construction projects.
But the types of houses they were building ran the gamut. High tunnels with double poly, gutter-connected glass, ebb-and-flood concrete floors, ECHOVeyor hanging basket lines … with just a snapshot look at a handful of growers building new facilities, it’s hard to really determine the latest trends in structures. So we decided to ask the suppliers to tell us the trends they’re seeing in the hardgoods market.
Size—and price—matter
The trends don’t really lean toward a “type” of greenhouse, but more on the side of what you can get with it. One theme that was the same with all of the greenhouse manufacturers that we spoke with: value. Obviously, price is a huge factor when a grower is considering building a new facility, but that’s not the only reason for choosing a specific type of structure.
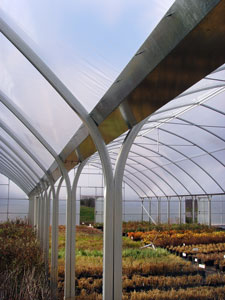
Gary Baze is sales manager for Golden Pacific Structures based in Redlands, California. His company is a division of Rough Brothers, an established greenhouse supplier that was looking to expand into other markets—specifically offering reduced-cost options to existing businesses, as well as to smaller and entry-level growers. So five years ago, Golden Pacific Structures was created to serve those markets. Gary said they started by offering hoop houses and Quonsets, but the business quickly evolved into gutter-connected cold frames, which is now their most popular seller.
Inside view of Golden Pacific Structures’ Windjammer series 6000 gutter-connected house
“Today’s growers are looking for the best value for their dollar, which is one reason we’ve had such a successful year,” Gary said. “The cost of our gutter-connected cold frames is very reasonable. Nowhere near the price of a traditional gutter-connected greenhouse. It’s a very low-cost option. [Another] reason I think we’ve been so successful is that it’s an easy product to build. It’s a very, very simple installation and in most cases, growers who are interested in this style of house typically can erect it them themselves, which is a huge advantage. And the third reason is that we offer some fairly wide houses—we go as wide as 35 ft. While stand-alone cold frames were where we got started and continue to be a big part of our market, the gutter-connected greenhouses have really taken off for us.”
The story is similar on the other side of the country. Atlas Manufacturing, Inc. in Alapaha, Georgia, offers a wide range of greenhouse structures and accessories to every level of grower. And owner Mark Davis agreed that price is key.
“I think a lot of that depends upon what kind of products they’re looking for, but I will say it does seem like everybody’s obviously interested in trying to come up with ways to save,” said Mark. “When it comes to the greenhouse, they’re certainly looking for energy savings. Of course, energy savings can then be grouped into whether you’re talking about heating or cooling, but they’re looking at ways to ultimately grow that crop and be more profitable.”
Mark says that his most popular product during the last few years is the freestanding cold frame that smaller growers tend to lean toward. It’s a cost-effective option that can be used to store stock plants and also for growing if it’s equipped with a heating/cooling system. For the larger growers, Atlas has sold many of their more economical styles of gutter-connected structures complete with curtain systems.
For the big guys, open-roof natural ventilation seems to be the “hot” thing. Many growers—especially in the south and west—have seen the advantages with this type of structure. Bill Vietas of Rough Brothers counts the reasons why open-roof houses are so popular.
“They use less operating costs because there are no fans running in the summer, so it makes for a lower electrical bill. There are somewhat less restrictions to the length of the greenhouse, fan-to-vent distance. And the plants are more acclimated to the ‘natural’ environment instead of being in a manually cooled greenhouse,” said Bill.
“We continue to see great interest in all of our naturally ventilated houses,” said Kenny Stuckmayer, commercial sales rep for Poly-Tex in Castle Rock, Minnesota. “We deal with a lot of wholesale growers looking for easy ventilation options. Our roll-up sides, ridge vents and Poly-Vents are popular with customers looking for simple solutions for ventilation.”
It’s what’s inside that counts, too
The true way to make a house a home is to fill it with your “stuff.” A greenhouse is no different, so Mark says growers should keep the total package in mind when purchasing a new facility.
“I think most of the manufacturers feel this way: The structure is only one component of the system,” Mark explained. “Ultimately it’s how it’s equipped because that’s where you’re spending your money going forward after the initial purchase of the range or the structure. Then you have to operate it. Depending on the type of crop that they’re growing, can they do that with natural ventilation? Or do they have to have the traditional fan, shutters, cooling pads, so on and so forth? That’s in the back of everyone’s minds.”
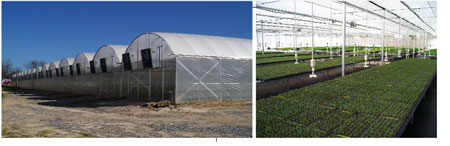
New gutter-connected greenhouses, one of Atlas Manufacturing’s most popular products, show how they look from the inside (right) and out.
This also includes the covering around the greenhouse. Although many retail growers still like glass because it offers more curb appeal, wholesale growers prefer the functional, more cost effective polyethylene or polycarbonate coverings for their houses. Depending on their crop, the possibilities are endless—they can choose single or double poly, and the type of light transmission they want, said Gary.
Having a variety of options also allows growers who perhaps can’t afford to build an entirely new structure to update the ones that already exist with new bells and whistles, said Mark. New shade/blackout/energy curtains, cooling systems or high-efficiency heaters (which are “beginning to be a buzzword,” said Mark), irrigation systems and other automation can make an antiquated greenhouse feel like new. Mark said many growers are choosing to update the inside rather than completely start from scratch because times have been tough the last few years.
“For most people, the structure is still dictated by budget. This would possibly dictate ‘skimping’ on some amenities or styles of greenhouse,” said Kenny. “Environmental controls are a big money saver, and affordable. With energy costs being volatile, controlling those costs is imperative. And shade/heat retention curtains are becoming more of a standard rather than the option.”
Times have changed
It’s interesting to look back at pictures of old wood-and-glass greenhouses (see A Look Back on page 22) that used to be popular and all of the manufacturers agreed that those are now pretty much extinct. So what else are growers looking for in a greenhouse?
“In the last 20 or so years, growers have built greenhouses taller and wider due to material handling and improved environmental considerations, which, I think, is a trend that’s continuing,” said Gary. “Fortunately, greenhouse manufacturers have been able to incorporate technology into their structures to meet evolving needs of today’s grower all while maintaining a reasonable price point.”
Mark agreed. “We’ve had just one customer who’s been our customer for years and has always bought the same type of structure,” he explained. “But the last two years, he has gone to taller and taller side walls. And again, it’s an effort to get that heat away from the crop, as well as the added benefit of having a more comfortable working environment inside the greenhouse.”
Another aspect of greenhouse construction that’s changed is the type of tubing used to build the structures. Historically, round tubes were used, but new technology has shown that square and rectangular tubing allows you to use fewer materials than with round tubing, while maintaining structural integrity. And since growers are going bigger and wider, square and rectangular tubing allows you to use fewer materials than with round tubing, said Mark.
So the good news is that there are more options available to build or update your growing structures, but the bad news is that it’s now harder to obtain financing to pay for it. As with the residential housing market, many growers—especially the smaller ones—have had trouble securing business loans, so many expansion plans have been put on hold.
“Initially when the economy went in the tank back in late 2007-2008, I do know it became a major obstacle that they couldn’t overcome,” said Mark. “Things got real tight, real quick and it all came down to this: we want to see your credentials, we want to see your profit-and-loss statement. I think things have improved in the financial market—not that we’ve had a rebound by any means—it’s just being eyed more and more closely. Now certainly, some people are doing real well and they are expanding. [The smaller grower] is the one I think was affected the most, but certainly I think at every level it had some impact.”
“We’ve definitely noticed an impact,” Kenny admitted. “But that has resulted in growers going back to the basics, wanting simple structures that are long lasting and require minimal maintenance.”
GT