5/24/2011
Three You Need
Jennifer Zurko
Want more from your water-quality meter? Do your transportation costs have you in tears? Is your labor laboring too much? Sounds like you need some new gadgets for your greenhouse.
Fortunately for you, we’ve found a few new tools to help make your operation run a little smoother. Each one covers the three Cs of many business investments: convenience, consistency and cost effectiveness.
The CleanGrow multi-ion sensor 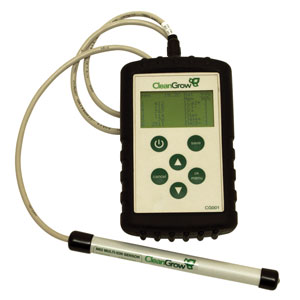
It was more Irish pluck than luck that gave Ciaran Long and Roy O’Mahony the idea for this groundbreaking ion sensor. The first of its kind on the market, the CleanGrow nutrient meter not only measures one ion, but can also measure five others at the same time. Ciaran said he and Roy founded the CleanGrow company two years ago as a way to support their interests in water quality and fertilizers. The company is based out of Cork, Ireland, but Ciaran has been living in San Francisco for the last 14 years.
As a plant scientist, Roy was able to use his knowledge to develop the CleanGrow multi-ion sensor, but neither he nor Ciaran—who has a background in finance and operations—knew how to introduce the product to the horticulture market.
“We were talking about various ideas and Roy mentioned Heiner Lieth’s book,” said Ciaran. A professor of environmental horticulture for the University of California-Davis, Dr. Lieth published a book called “Soilless Culture” in 2007. Since the professor’s office was close by, Ciaran decided to drive to Davis to talk to him about the CleanGrow product and ask his advice.
“We were very open with our ideas,” said Ciaran. “We just took feedback that we got from Professor Lieth and lots of other people, and based on that, worked out what would be the best approach.”
The CleanGrow product features the first-ever combination of a carbon nanotube-sensor with a multiple-ion meter. It’s a hand-held style—which most growers are familiar with—but instead of relying solely on pH or EC measurements to determine your nutrient levels, the meter can measure up to six ions simultaneously from a total of 18 different nutrients.
There is a six-ion meter that measures Calcium, Chloride, Potassium, Sodium, Ammonium and Nitrogen; the four-ion probe can be any combination of these six ions. CleanGrow comes in a package that includes the meter, PC software that allows you to manage the sensor and extract saved data to upload into an Excel file, and access to a website where you can store your data and look at historical trends, including high and low values.
“It’s a product that I think the industry’s been waiting for,” said Dr. Lieth, who has been the primary “tester” of the CleanGrow sensor for his own growing and research. “Largely because for nutrient management, there’s all this stabbing in the dark, and when we adjust nutrient regimes in the greenhouses on our crops, we invariably are doing it with information that’s two weeks old. So this product is one that really promises to change things.”
The CleanGrow system is so new that it hasn’t even been introduced in the U.S. yet. Its first unveiling was at Horti Fair this past year, when the sensor was nominated for the Innovation Award—the only non-Dutch company to earn a nomination. Ciaran and Roy will have a booth at this year’s Short Course where North American growers can see it for the first time.
And it’s so new, Ciaran said that he and his team are still working out some of the elements of the user interface “to make it even easier for growers to use it.” The final prototype has been tested in the market since February and so far the response has been excellent, said Ciaran.
“Growers can’t afford to send samples to labs constantly and even if they do, it takes a period of time to get that information back,” Ciaran explained. “It’s time and money, so people really want to be able to find out what’s going on with their nutrients constantly. Really, they’re limited to just measuring EC at the moment, which is kind of a crude representation of what’s going on with each nutrient. So we’re just giving them real-time access to some very powerful information that they can use to increase yield of their crops.”
“The reality is if a grower makes one serious mistake with nutrient management, it’s going to cost thousands of dollars,” said Dr. Lieth. “So if this device can prevent one of those, it will have paid for itself.”
To see a video demonstration of how the CleanGrow multi-ion sensor works, visit
www.cleangrow.com.
Z Beam Shipper Display Racks 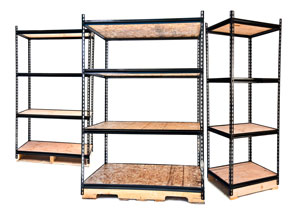
Those who have been in this business for years have devised their own system of delivering their products to their customers. With fuel and shipping costs at an all-time high, many growers have been re-evaluating how the transportation part of the business is impacting the bottom line.
Since 2000, the EZ Shipper Racks company has offered a rental-and-recovery program for growers that allows them to ship multiple levels of product on one rack with the convenience of not having to worry about picking up empty racks from the stores. EZ Shipper Racks delivers the rack to the grower, who assembles it, fills it with product, puts it on the truck and delivers it to the store. Once the rack is empty and placed outside of the store, EZ Shipper Racks comes out to pick it up and brings it to one of their 65 repackaging centers so it can be broken down and sent to the next grower who needs one. Ron Sims, who handles sales and marketing for EZ Shipper Racks, says that more than 200,000 racks are recycled every year.
Adam Stewart, executive VP for Bell Nursery in Burtonsville, Maryland, says they’ve been using the EZ Shipper Racks for the last five years. One of the reasons they use them is because they can handle heavier materials, like shrubs and trees, which can damage a regular cart.
“You can ship gallons and three gallons on an annual cart, but once they’re wet, they start to weigh down the shelves,” said Adam. “[EZ Shipper Racks] get a much better payload than other racks and they’re also more conducive to loading on a semi. It’s also good when we’re going to remote locations and we don’t want to have to circle back to pick up the carts. EZ Shipper just does it for us.”
Their newest product—called Z Beam Shipper Display Racks—is a low-cost solution that will meet the demand of independents, and even other retailers outside of the industry, that are looking to buy a more permanent display structure that is strong enough to handle up to 500 lbs. of product, but can be moved easily with a pallet jack. The Z Beam racks are not part of the rental-and-recovery program, but rather a separate system that is available for purchase and comes in three different pallet sizes—quarter, half and full. Also, the racks themselves are made with less material, keeping the weight down. The steel infrastructure and adjustable wood shelves are durable enough to hold up to many conditions—like plants that are watered daily.
As with the rental racks, the Z Beam racks don’t have wheels, so there are less liability concerns with racks tipping over or cruising through the garden center on a windy day. The grower or retailer also doesn’t have to invest in special trucks with E-Track; the racks stay put once they’re loaded on the truck. And the ease of unloading the racks allows you to unload the equivalent of 25 pallets in about 10 minutes, said Ron.
Jeff Salmanson, one of the owners of EZ Shipper Racks, says that it all boils down to getting the most payload per shipment. “Transportation is one of the most expensive parts of a nursery. We’re starting to get more and more people analyzing their payload needs and we’re starting to get more and more people that are looking at us because we do get a really full payload. I don’t believe there are very many racks in the whole industry that will maximize the truck the way ours will.”
ECHO Veyor
Most growers know about the ECHO automated basket irrigation system, but what you may not be aware of is Cherry Creek Systems’ current work on the next stage of cable transport systems, called the ECHO Veyor, that helps growers easily move product in and out of the greenhouse.
Cherry Creek’s General Manager Chris Lundgren said that owner Arie Van Wingerden came up with the ECHO Veyor idea when one of his brothers was looking for a way to move plug trays from the germination room to the greenhouse. Arie took elements from the ECHO basket system and developed a conveyor-type system that would move the trays easily and quickly. From there, the ECHO Veyor evolved from a two-cable system to the latest 10-cable version that was just installed for Dutch Heritage Gardens in Larkspur, Colorado.
“The whole goal behind the ECHO Veyor was to build a product transportation system that would not cost as much as a conveyor belt,” explained Chris. “And we’ve made improvements along the way just based on the fact that it started with two cables and now we’re actually at 10 cables across, trying to get as close as we can to a conveyor belt.”
Chris listed the many advantages of the ECHO Veyor, like the fact that you can grow crops underneath it and it’s very durable. One of the drawbacks is that the ECHO Veyor isn’t mobile like some conveyor belts because it runs on a tension system. However, the cost of the ECHO Veyor is much more reasonable—especially since the new 10-cable version carries small pots, as well as flats, trays and hanging baskets, while handling the weight without slowing down. Chris says the price averages about $30 per lineal foot, which is a third of the cost of conveyor systems.
Recently, Ivy Acres in Baiting Hollow, New York, built Haygrove PolyTunnels that included 11 ECHO Veyors across 22 bays reaching 540 ft. end to end, said Kurt Van de Wetering. He chose the ECHO Veyor because it alleviated the need for concrete cut-throughs and half-ways for carts and tractors. They also needed something to withstand the changing temperatures because the tunnels remain uncovered during the winter.
“Once we got the tensions right, we could really pack out a large quantity,” said Kurt. “You can put the product pot-to-pot and it takes that load all the way across. And these are long spans. It has no problem with the amount of weight that comes through.”
GT