2/21/2011
Greenhouse Efficiency: Pushing Productivity
Jennifer Zurko
Do your old boom systems have you wringing your hands? Are your thermostats not playing nice together? Is hand-breaking soil bales driving you past the breaking point? There’s an app for that.
Not a smartphone app (wouldn’t that be nice?), but convenient—and economical—applications that provide solutions to many typical greenhouse problems. Read on to see how some new systems and products helped a few of your peers with their growing business.
Go with the flow
Give yourself options. That’s what Glenn Harrison, head grower for Cavicchio Greenhouses in Sudbury, Massachusetts, did when they were forced to rebuild 2 acres of greenhouses after a fire destroyed some of their 20-year-old facilities. Glenn and third-generation owner Paul Cavicchio, Jr. sat down and figured out what they needed to make the new greenhouse even more efficient than the previous facility, which wouldn’t be a difficult task since the irrigation in the old houses was primarily done by hand, with the original booms handling the rest.
Glenn Harrison, head grower for Cavicchio’s Greenhouses, kneels on the state-of-the-art TrueFlow floor, an ebb-and-“flow” system that uses less water and offers less risk for disease.
Glenn estimates their productivity will increase with the new irrigation and heating systems. The green and white pipes in the background are the valves that control the TrueFlow system.
A brand new type of subirrigation system from TrueLeaf Technologies, called TrueFlow, was included in the construction of their new greenhouses after Glenn saw it at other facilities in Canada. Unlike ebb-and-flood floors, which are shaped like a V or W and fill and drain from the center, a TrueFlow ebb-and-flow floor is angled from one post row to the next. It fills from one edge, and runs across to the drain on the low side like a river; sort of like ebb-and-flood trough benches, but on a very large scale.
After doing some more research—which included going back up to Canada and trying the a similar system from ZWART using Cavicchio pots—they were convinced that this was something they wanted in their new facility.
“The reason was two-fold: conservation and efficiency,” said Glenn. “It’s the whole reason you would go with any kind of flood floor to begin with to reduce labor for watering and also water conservation and the ability to re-use.”
The amount of water that’s used allows Glenn to utilize the new houses for a multitude of crops—including those that would traditionally be run on the drier side. “The benefit is you don’t have to water to a full container capacity like you need to with a flood-floor system,” Glenn explained. “The amount of water applied to a crop has an impact on plant habit, disease susceptibility … it really can determine the overall quality of the finished product, and this system gives us that control.”
Most of the water for the new system will be collected rainwater, which is a first for Glenn. “It’s going to be interesting to learn the ins and outs of the growing side of using rainwater. The alkalinity is much different from what I’m used to and it’s certainly a much more pure water source.”
Morris Brink, VP of West Coast sales for TrueLeaf, said that the TrueFlow system is based on the concept of “sheet flow” because “the floor is slanted, where one point is the high point and then there’s a low point. It fills up from the high point and it creates a ‘river’ that flows down to the bottom. There’s some great engineering behind it and we’re really excited to see what Cavicchio’s thinks of it.” This allows for more even watering for every pot, whereas with traditional ebb-and-flood systems, sometimes the pots in the middle get more water. The TrueFlow system also gives the grower the ability to set the flow duration, depth and speed.
Another aspect of the TrueFlow system is the underground heating, which dries the floors after watering to prevent disease and keeps the root zone warm, said Morris. And TrueFlow actually costs less than most traditional ebb-and-flood systems, depending on the size of the growing area.
Cavicchio’s Greenhouses is the first U.S. commercial grower to try the TrueFlow system. “In a way, we are kind of the Guinea pigs, so it’s a little bit nerve-racking,” Glenn admits. “But I feel like we’ve done our homework enough that we’re confident in what it’s going to do for us.”
Since they’re is still putting the finishing touches on the new facility, Glenn hasn’t had a chance to actually try the TrueFlow floor out himself, but he’s anticipating learning how it’ll work for their crops this season. The new greenhouses also include drip irrigation for hanging baskets and truss-style booms. “While this new flow system does improve versatility, there are always going to be things that require some type of overhead irrigation and having those booms saves a lot of time,” he said.
Since the fire, Glenn has had to scramble to replace the precious growing space in time for this spring’s crop, but he looks at it as a good learning experience and a chance to grow in a brand new, state-of-the-art greenhouse.
“It was a huge loss, no question, but in some ways, it’s kind of a blessing in disguise,” said Glenn. “This is definitely an upgrade from what was there before.”
Take control … of everything
For many growers, it’s not specific products that offer more efficiency, but systems. This is where control systems companies like Argus (based out of White Rock, British Columbia) and Wadsworth (Arvada, Colorado) come in.
When Lloyd and Candy Traven started Peace Tree Farm in Kintersville, Pennsylvania, in 1983, all they had to control their greenhouses were five thermostats mounted in a wooden box. In 1988, the Travens were the smallest commercial grower to install an Argus control system.
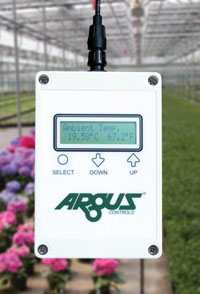
“We went full tilt,” recalls Lloyd. “We had it take over all of the irrigation, as well as all the environmental controls, misting, everything, in one fell swoop. Out of all the decisions we’ve made—both good and bad—it’s probably been the best we ever made.”
Since the original control system was installed, Lloyd has been able to add and improve on it. They revamped the heating system in one of the older greenhouses in 1998, and in 2004, built new glass greenhouses, which now holds the entire control system for all of Peace Tree Farm’s facilities. Lloyd says it offers a multitude of benefits, not only with labor, but also with the ability to program his crops.
“First of all, for irrigation control, you can have one person do an entire range by themselves very effectively,” said Lloyd. “That’s a huge savings for us. The second is that our environmental controls are spot on, so when we want gerberas to finish on a specific date, we set the temperature regime that gets us there.”
The control system also allowed Lloyd to more than double the size of his operation (which now totals 60,000 sq. ft. of growing space) without having to add additional labor right away.
Both Argus and Wadsworth provide growers with greenhouse system integrations—which includes (but, of course, is not limited to) heating, ventilation and irrigation. Wadsworth offers services for smaller growers who may not be able to afford a large system, including motors and curtain systems, said Amanda Debevc, sales and marketing manager for Wadsworth. “The smallest control system starts with just a few hundred dollars and then we go up from there,” she explained. “So what we’ve tried to build are control systems that fit everybody and have some features that are very similar to the integrated high-end control systems with the simple concept of just basic heating and cooling controllers.”
And because each growing operation is different, each request is managed individually. The standard pieces of the control function are always there, but each system is able to “bend and mend” to fit the needs of the specific grower and the type of facilities they have so they can grow the best crop possible, said Amanda.
“Think of us like a buffet,” says Alec McKenzie, director of research and development for Argus. “You can go down the line and build yourself a meal that’s to your tastes off the same line that everybody else builds their meals from. Everyone gets a unique custom meal, while the chef only had to produce the stock items in efficient volumes.”
On the smaller side
For those growers that don’t have a large operation, but are looking to make life a little easier, S.B. Machinerie recently introduced the SB05—a manual soil mixer, bale breaker and manual flat/pot filler designed with the small grower in mind.
“I love that thing!” exclaimed Theresa Freund, owner of Freund’s Farm Market in East Canaan, Connecticut. “It has completely changed who can do the job of filling pots and flats. It used to be you had to hire a strong, strappy guy to break the bales and we were doing it by hand. Now I can give the job to my oldest employee as long as the bale is already loaded.”
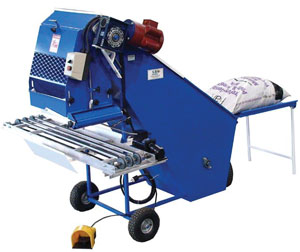
Dan McMahon, hardgoods business manager for Ball Horticultural Company—who is the exclusive distributor for S.B. Machinerie—said that the SB05 has become a popular item with small growers. Measuring at 36 in. x 5 ft. x 5.5 ft., its size offers a lot more versatility for growers like Theresa, who says she’s able to move the SB05 around her small 12,800-sq. ft. growing area. During the last two seasons with the SB05, Theresa’s team has been using less energy by not having to carry filled pots through different parts of the greenhouse. And with a capacity of 0.70 cu. yd. that breaks up 3.8 cu. ft. compressed bales using a chain system, Theresa said that she can easily add water for proper moisture, along with biocontrols.
Another plus for the SB05: it’s inexpensive (about $6,200), which is why Theresa decided to buy it when she attended the New England Grows show.
“When I looked at the other pot-filler machines, they were always way over the $20,000 price point and when I look at what I’m paying an employee to do the job, you have to ask ‘what’s the pay-back?’” said Theresa. “[The SB05] is the best machine for the job. When you think of all the heavy, back-breaking things you have to do in a day—if that is the one thing that you don’t have to dread anymore—it’s worth it.”
To see a video of how the SB05 works, visit
www.youtube.com/watch?v=RcFmJ9NGItM.
GT