2/21/2011
Nieuw Glastuinbouwprojectens (New Greenhouse Projects)
Chris Beytes
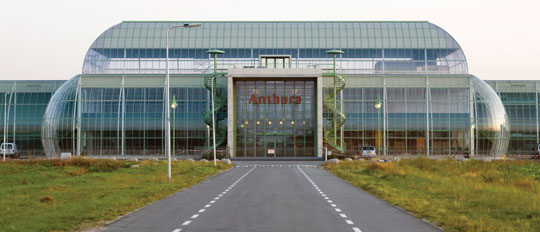
Anthura
The world’s largest anthurium breeder and young plant supplier now has the world’s prettiest production
greenhouse.
“It is actually a normal greenhouse, from one point of view,” explains Anthura’s export manager, Rick Kroon, as we sit in the facility’s comfortable canteen having the requisite coffee before taking a tour. “On the other hand, it’s a “nice” greenhouse, and that I think is what makes the difference.”
That “difference” is an exterior design that mimics the classic Victorian greenhouses of the Royal Botanical Gardens, Kew, in England. From the curved glass and powder-coated “verdigris” finish, to the soaring dome over the entrance and vintage-style lights in the expansive foyer, Anthura’s new facility is a showplace of the greenhouse manufacturer’s art.
Anthura had three goals with the new greenhouse: labor efficiency through centralized production and automation (formerly, they were spread across five locations); energy efficiency, meaning less use of energy per plant, less use of water per plant; and a nice working environment … and as Rick says, “It doesn’t get any nicer than this, I think, greenhouse-wise.”
And, one more goal: show the world that a greenhouse can be a good neighbor—both visually and from an energy use and conservation standpoint.
“All of that came together in this building,” says Rick.
Rick says their first discussion was, do they even stay in the Netherlands? They actually discussed China, the United States … any location was on the table from which to supply the global market with anthurium young plants. But the question was settled: Stay at home in the Netherlands.
That meant a big greenhouse: 30 acres in the main greenhouse, plus 5 acres in a second level over the potting and sorting area. Built by Van Der Hoeven, the actual production greenhouse is quite ordinary, although big: 30 ft. to the gutters, with the decorative dome reaching almost 50 ft. high. The Dutch trays are also 30 ft. wide, meaning each bay is more than 60 ft. wide (42 ft. is more typical). The growing area is divided into six 5-acre zones.
One interesting internal component is a “greenhouse-in-greenhouse” concept—basically a “tent” inside the two of the six zones, in which Anthura starts off their young plants.
Another unique feature is a double layer “shutter-style” shade curtain system that allows for quickly changing the shade over the crop from 50% to 100%, allowing the computer to react more quickly to Holland’s fast-changing light conditions. (The house also has a typical energy curtain.)
For labor efficiency, they installed a one-off young plant grading machine by Flier that has dramatically reduced labor for that task. Overall, this facility has 200 employees, vs. 300 for their five scattered locations.
“This way we were able to lower our overall costs and stay in Holland,” Rick says.
Like other new Dutch greenhouses, they use cogen plant (3.5 megawatts) for electricity and heating, selling excess electricity to the grid (in 2009 they generated enough extra juice to serve 2,000 households—part of being a good neighbor). They are also using underground storage of warm and cool water to help heat and cool the greenhouse. Water is stored at a depth of 500 to 600 ft. beneath the greenhouse and is pumped up as needed—amazing technology.
But it’s the stunning exterior that gets all the attention.
“It’s always been a desire of the founder of the company, Nic van der Knaap, to prove to all the other stakeholders that a greenhouse can also be something nice,” explains Rick. “He was inspired by the botanical greenhouse at Kew Gardens (in England). He’s made an entire study of it; he’s been thinking about it, I think, for over ten years, and he decided it should be a curved greenhouse.”
The curved portion is really just a façade for the production greenhouse. But in addition to being beautiful, it’s also functional: The three curved sides are corridors where most of the technical equipment resides. This keeps workers out of the growing area (we weren’t allowed in either, even though we were wearing Tyvek suits), helping reduce the risk of contamination (anthurium is very susceptible to diseases).
The decorative dome houses a 300-seat conference room on the third level. The spiral stairs on either side of the entrance are meant to mimic the double helix of DNA, visually linking tradition with technology.
So, what’s does all this beauty and technology cost?
“I’m not at liberty to say,” Rick says with a smile. (He also wasn’t at liberty to allow us to publish photos of the production or growing areas.) But he points out that the pretty part of the greenhouse amounted to only a very small percentage of the total cost.
And back to the “good neighbor” image thing: How has that worked out?
“Beyond expectation” he answers. “We could make it a tourist attraction. I think we could be fully booked.” They’ve given tours to everyone imaginable: students, businesspeople, government officials, the press, foreign diplomats—“the secretary of the Chinese politburo was here in September,” Rick says.
“Queen Beatrix?” we ask.
“No, she hasn’t been here,” he admits. “But she’s welcome!”
www.anthura.nl
Ter Laak Orchids
If you’re located along a major highway, why not turn your building into a billboard? That’s what Ter Laak Orchids has done along the N211 in Wateringen: Carved into the side of their new 20-acre orchid range in massive letters is their business and family name, Ter Laak. It shows the length to which modern Dutch greenhouse operations are marketing themselves and their products (see Anthura, above).
Brothers Eduard and Richard ter Laak are definitely doing more marketing these days, which we’ll talk about in a second. But first, the greenhouse:
Like Anthura’s, it was built to consolidate multiple locations (three) into one. Like Anthura, it was built to maximize labor efficiency (30% improvement over their old ranges) and energy efficiency (10% improvement). And it was built to showcase the company as an innovator.
Right: With a sign like this, there’s no mistaking where you are. Left: Eduard with his father, Eduard Sr., who first got the family into the orchid business. He still comes into the nursery every day.
The Ter Laak family started in the vegetable business 45 years ago, then moved into cymbidium orchids, first cuts then pots. The were one of the first growers to enter the now-competitive phalaenopsis business.
In the early 2000s, they began acquiring land near around their existing facilities, with the goal of eventually building one master location. They eventually bought out nine older nurseries, plus some bare land, to build a 16-hectare (40-acre) site.
“We’ve been thinking for years how to do it,” Eduard said of their clean sheet of paper. “You do it maybe once [in our career] at this size.”
For them, it’s all about growing a plant for the highest market segment—that means large and beefy, with strong stems and lots of flowers. That means light and space and time (some 80 weeks from TC liner to finished plant). So anything that would speed up the crop or reduce labor while still maintaining top quality was considered.
The greenhouse, by Technokas, is fairly standard: 13.5 acres of ground-level Venlo-style growing space, plus 4 acres of widespan growing space above the potting and packing area. Gutter height of the Venlo house is 21 ft., while the widespan area is 30 ft. to the gutter. Including the service rooms for heat and water, the facility covers almost 20 acres.
Bays are the standard 12.8 meters (42 ft.) wide, and the tables are more than 6 meters wide (two per bay), so there is no aisle space at all. Crops are checked by the grower by catwalk-equipped booms.
A unique but subtle feature is that the Venlo gutters run perpendicular to the widespan gutters, making construction a challenge. Eduard explains that they did that in order to run the internal logistics just how they wanted. Why not use widespan for everything? “We’ve always grown in Venlo,” he answers. “For us it's good, and cheaper. Widespan is much more expensive. And we also wanted to have outside screens. With widespan, the outside screen is on the glass, this is above it.”
That outside screen is for shade—it’s the sort of system you’d more likely find in the tropics. The exterior shade screen eliminates the need for painting the glass every spring, which is a labor and safety issue, and results in uneven shading at some times of the year. “Plus, there are dark days when you don’t want it, and sunny days when you need screening,” Eduard adds. “The outer screen is perfect.”
Above the spots where the outside screen folds up, there will be long, narrow solar panels. Eduard says they will make a little bit of energy with them—enough for office lights and pumps and such—but it’s also for the image that solar power brings—and to be a test bed for this emerging technology. “I hope that in five or ten years we’ll have solar panels built in to the screen,” Eduard says.
For orchid growing, Ter Laak uses “plant growth cells”—clear plastic cups in which the orchids reside while growing. The cups hold the foliage up, preventing plants from tangling or shading one another, and allowing more plants per square meter. It has become standard orchid-production practice.
But Ter Laak has added a second, larger plant growth cell for the last part of production, when orchids are starting to spike. This gives the plants a bit more room and supports the flower spikes as they develop. Plants are put in and taken out of the cups by automatic equipment. As with most Dutch pot plant greenhouses, computers and video cameras grade the crop at every step in the production process.
This will allow Ter Laak to produce four million 12-cm (4.75-in.) pots per year—a more than 100% increase from before, when they were doing 1.8 million per year. And they’ll produce them at the same quality, or higher, than before.
Eduard says they could use smaller cups and get a tighter spacing and more finished plants, but “But because we go for the quality, we need a wider cup. There are growers with smaller cups who can grow more. But they make another [grade] of product.”
Once plants are graded for the final time, a computer sorts the finished plants onto belts and then into orders, which are automatically sent to the nine packing lines. They do have one sleeving/traying machine, “but especially with our high quality, that part of the market asks for more,” Eduard explains. “So you have to do a lot to the plant–price labels, extra labels … .” They have cut labor by 30%, down to about 50 employees. But as he says, their level of quality will always demand more human touch.
Cost of the project? About 32 million Euros ($43.5 million). And that’s without the land. You’d think that note would keep him up at night, but no. It’s actually marketing.
“Years ago it was producing, producing. And now you have to think about how you’re going to sell it, how you’re going to be different than other orchid growers. Because everybody can produce phalaenopsis.”
To that end, they hired a marketer to help them develop a new logo that describes their business. It’s a large “123.” The 1 is for ambition, the 2 is their respect for nature and people, and 3 is for keeping it simple. Even the design of the building reflects those elements. A glass-walled courtyard with planted trees shows both their love of nature and their transparency.
“We don’t want to be arrogant,” Eduard explains, “we want to be good … but now we want to tell our story more.”
And about that giant logo carved into the building?
“Yeah, you have to show the people who you are and what we do. Our business name is Ter Laak. Our family name, too. So that’s why we put it on the front of our company.”
www.terlaak-orchidee.nl
GT